The automotive industry is changing and so is Formula SAE, which is increasingly turning to electric thanks to the growing number of teams that decide to compete in this class that is both present and future-oriented.
An opportunity for growth in a sector that has seen accelerated development, also for the students of Formula SAE, who use the competition not only as a chance to try their hand at an experience that allows them to put their theoretical university studies into practice, but also as a chance to increase their skills directly in the field together with many colleagues.
A technical and management adventure that Motorsport.com explored with Enrico Dal Bo, Team Leader of the “UniUd E-Racing Team” of the University of Udine, whose first experience in the Formula ATA in Varano a year ago, made up of solutions to overcome the challenges of electric and a lot of passion for a project that started from a blank sheet of paper. Twelve months later, the students have made the most of what they have learned in the tests and in the various competitions in which they have taken part with the aim of improving their prototype and making it even more competitive. A journey that has led them to show up in Varano with a completely renewed vehicle compared to the 2023 one.
Formula SAE 2024 – UNIUD E-Racing Team
Photo by: Luca Baldassi | UNIUD E-Racing Team
This is your second year in Formula SAE. Compared to the first year, what improvements have you made to the car and how many events have you participated in to be prepared for the Varano event, considering that the calendar has been revised by moving the Italian stage to September?
“Last year we took part in two competitions, Formula ATA in July and then Formula Student Spain at the beginning of August in Spain on the Barcelona circuit. In addition to these events, we conducted various types of tests that allowed us to verify the behavior of the previous vehicle based on what we had designed last year. Once the events were over, in fact, we analyzed all the data collected from the various tests and competitions to think about how to develop the new vehicle, which is completely different this year. Some components of the first prototype were recovered to build this new vehicle, while others such as the chassis, the body, the cooling system, the hub carriers and the rockers are completely new and developed based on the data collected. The new vehicle is 101.4 kg lighter than the previous one, so about 25% less. In fact, our big challenge was to improve the weight because, from what we understood in past editions, our prototype was oversized due to some safe choices that, at that time, could have allowed us to compete”.
In which areas did you find the greatest weight savings? The cooling system and the battery are areas where there is certainly room for development.
“We found a great weight saving on our vehicle’s battery. In September last year we won the Tesla tender again which allowed us to have a new supply of cells completely free and sponsored by Tesla together with the BMS chips. We redesigned the entire battery pack, which last year was made of steel because we wanted to build the vehicle quickly and it was the fastest and most effective choice in the conditions we were in at that time. This year, however, the battery pack is entirely made in our laboratory with a lamination of Kevlar skin and has ten modules instead of the twelve of the previous one. This allowed us to go from a weight of 90kg to the current 55kg of this year’s battery pack mounted on the new prototype. Another important weight reduction is found on the cooling system. In fact, one of the first tests we did after returning from the competition in Spain concerned precisely this aspect of the car, using various temperature sensors in the cooling system that measured the temperature of the flows entering and exiting the engine, inverter and radiators. In the end, we opted to put two smaller radiators on our vehicle rather than the single one on the old prototype.”
One of the new elements this year is definitely the front wing that steals the attention as the most visible novelty. A choice that, as you told us, represents the first step towards a complete aerodynamic package optimized for your car.
“We have studied a solution that would allow us to increase the downforce of the vehicle, as our prototype has the weight shifted mainly towards the rear on the rear axle behind the driver, where we have the battery, the engine and the transmission. The additional load at the front guarantees greater stability and confidence for the driver when driving, but we are aware that this only happens in certain working conditions and at specific speeds. In fact, it is only a first step, because the final objective is to develop a complete aerodynamic package, with front and rear wings, designed and optimised specifically for our car. We have therefore designed this intermediate solution, so as to arrive at next year with much more advanced know-how, which will allow us to integrate a rear wing next season. Furthermore, having a front wing also allows us to work on the management of the air flow that meets the vehicle and the front wheel group, directing it towards the areas we want, such as the cooling system located in the rear”.
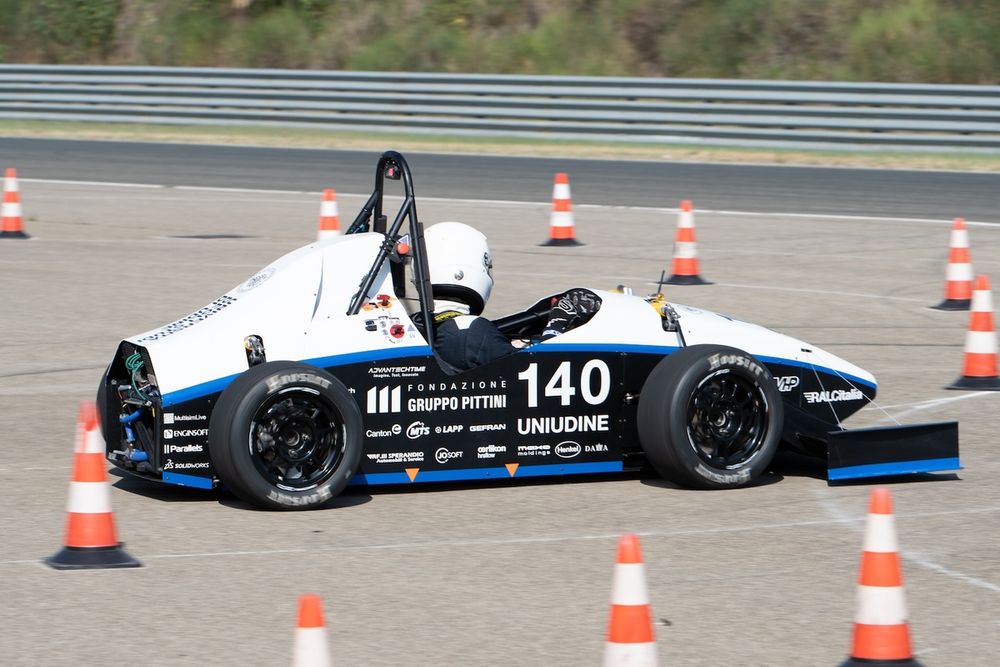
Formula SAE 2024
Photo by: Davide Cavazza
When you started working on this project, you told us that you had considered different ideas, finally focusing on the electric prototype, even though designing a combustion vehicle would have had a significantly lower cost for a first-time team. Yours was a choice aimed at a long-term project, which seems to be also more effective, also considering all the knowledge acquired and the progress made in the last year.
“Yes, in this type of competition, like Formula Student Germany, the combustion engine is in its final years. This year we took part in the German competition, where there were no combustion teams since it was only intended for electric vehicles. Formula Student Germany is a bit of a reference for other competitions and for us it was a big achievement to be able to participate. Our team could have chosen to start with a combustion engine which would have been much simpler both from a budget and management point of view, because in fact you go and buy a complete engine, and then do some work to adapt it to the vehicle and, perhaps, improve some of its characteristics. However, the control is essentially not the same as the control we have in an electric engine where we have to design completely different and more complex boards and circuits than those needed to manage a combustion engine, which does not have the same difficulties as an electric engine”.
So, beyond the fact that the automotive world is moving towards electric, it also represents an opportunity for you students to acquire greater knowledge and deal with increasingly broader and more complex challenges.
“There are certainly many more studies and complexities in an electric project than a combustion one, at this time, also related to the management of the battery pack. We would certainly have encountered some common difficulties at the beginning of the journey even with a project with a combustion engine regarding the dynamics of the vehicle, but within a year or two from now we would still have had to deal with the transition to electric.”
Many teams here are focusing on energy regeneration systems, including you.
“Yes, we have an energy regeneration system that essentially regenerates electricity when the vehicle is braking thanks to the engine and the inverter that are in our vehicle.”
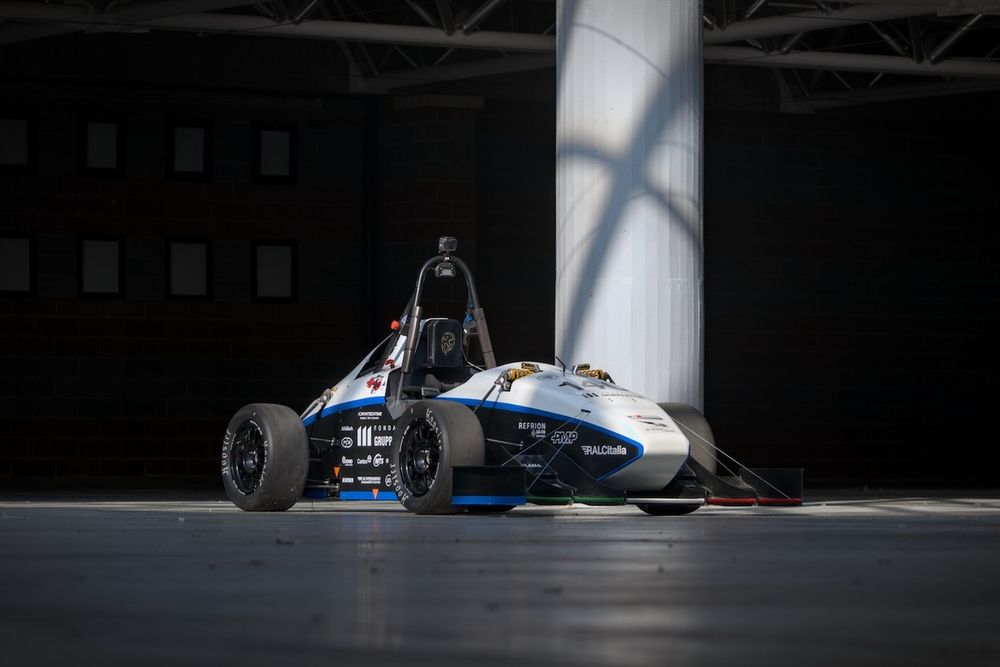
Formula SAE 2024 – UNIUD E-Racing Team
Photo by: Luca Baldassi | UNIUD E-Racing Team
From this point of view, one of the most important challenges is the management of the heat of the energy arriving at the battery from the regeneration system?
“We have done several simulations using our design software like Siemens STAR CCM+, where we run several worst-case analyses, like with the battery modules stressed to the max, and rest assured, we have found that our battery pack cooling can handle these loads and discharges of the pack.”
When is it difficult for a team and a Team leader to find opportunities at the sponsor level? You have worked hard in the last year to redesign a large part of the car and, clearly, this has a higher cost for you in terms of research, development and design. Teams that have been competing for many years and have a consolidated base perhaps start to work more on the details and the costs are reduced.
“When we look for sponsors and companies that want to support the project, the difficulty lies more in obtaining confirmation of a sponsorship from these companies rather than interest. Most companies are always interested in the project and are always available to listen to what we have to say. Sometimes, however, we do not reach an agreement that allows companies to collaborate with us and therefore we encounter some difficulties. Starting from an established base is certainly much simpler than building a vehicle from scratch, also because we are talking about the creation of a single vehicle, a prototype, so the costs are very high. We are not talking about a mass-produced vehicle in which you can have the advantage of buying large batches of product and therefore have discounts on the quantity. By buying a few components from the catalog, given that most of the products in the vehicle components are designed by us, the costs go up and therefore starting from an established base is always easier than improving and modifying your project every year”.
One of the great aspects for an electric prototype is also the work at the code level, which is continuously improving.
“We definitely have more work to do than the combustion engine that already has its own control unit when you buy it from the factory. Of course, we always start from the datasheets of the components we buy, so we always start from the base of the data that the engine wants and the data that the inverter needs. From there we start, we do the programming. Our team stands out for the fact that this year too we are the only team in Formula ATA and among the few in the world to use a totally different and modern programming language, RUST. In fact, last year right here in Italy we were rewarded for the fact that we had developed a telemetry and software management system for our vehicle with this completely innovative and much more dynamic language”.
Thanks for your availability and good luck for the next challenges to the students of UniUd E-Racing Team.
#Formula #SAE #role #experience #win #electric #challenge