The new one Dacia Dusternow in its third generation after almost 15 years and over 2.4 million units sold, of which 330,000 in Italyis produced in the Dacia plant in Myvenea production plant located in Romania with decidedly cutting-edge production lines for bodywork, mechanical and engine parts.
Dacia Duster, the factory where it is produced
The Mioveni plant in Romania is one of the most advanced and efficient of the Renault Group where the new Dacia Duster is produced. It covers an area of 288 hectares with a daily production of the order of 1,400 vehicles. A car rolls off the production line every 55 seconds. The plant operates in three shifts and produces approximately 350,000 vehicles per yearsold in 44 countries. Among the vehicles produced, 65% are Duster, 25% Jogger and 10% Sandero Stepway and Logan, these are the production data from last year to June 2023.
The plant employs approximately 7,000 peoplewith a strong female presence, and combines advanced automation with human intervention to ensure high quality. The plant also includes a press department that produces 280,000 body parts per daythanks to an investment of over 35 million euros.
The numbers of the Dacia factory in Romania
The cars produced by Dacia are distinguished by their concreteness, practicality and competitive pricewithout sacrificing robustness, quality and reliability. This advantageous price-performance ratio is made possible by a highly efficient production processwhich minimizes waste, such as reusing waste materials to create smaller components.
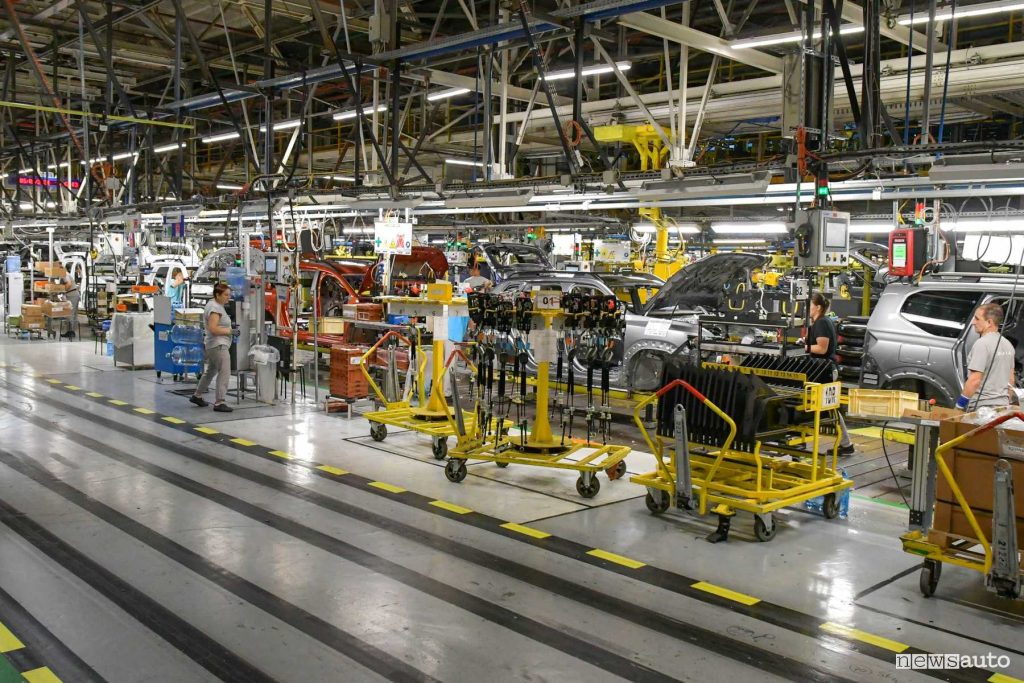
On the 1,200-meter-long production line, there are 172 vehicles being assembled at the same time, from the first workstation to the end of the process. Over 1,800 specialists are employed in seven dedicated laboratories, a maintenance laboratory and one for the development of new projects, involving a third of them women. Quality control, entrusted to a team of 243 experts, is distributed along the entire line and in every phase of the production process. 80% of the team is dedicated to direct checks on the vehicles, while the remaining 15% carries out supervision and data analysis activities.
There are 800 checkpoints for four body types, various engine and transmission types and different equipment levels. The inspection time for each vehicle in the “quiet room” is 15 minutes, while the functionality, external and internal appearance and multimedia functionality are checked. After assembly, each vehicle is subjected to a series of thorough checks in special inspection cells. There are 800 checkpoints for four body types, various engine and transmission types and different equipment levels. In these areas, the functionality of all components, the internal and external aesthetic aspects and the correct functioning of the multimedia systems are checked. The inspection process lasts approximately 15 minutes.
To ensure maximum precision, state-of-the-art measuring instruments and specific test benches are used to adjust the parallelism, headlight alignment and driver assistance systems. In addition, each vehicle is subjected to a simulated road test to verify the correct functioning of all electronic systems.
Bodywork parts, mechanics and plastic moulding production department
In the press shop, the newest section is the high-speed zone, an investment of 37 million euros, completed in 2020, where aesthetic parts are made: door panels, front hood, roof. Depending on the complexity of the assortments, the high-speed line can produce 9,600 parts in an eight-hour shift. Currently, mainly series parts for the Duster, Jogger, Sandero and Logan models are produced.
The body shop employs 1,800 people, engaged in different production phases. There are two identical assembly flows: one is dedicated exclusively to the Duster model, with a capacity of 40 vehicles per hour, while the other handles Jogger, Logan, Sandero Stepway and Duster, with a capacity of 35 vehicles per hour. The shop has 556 robots, with an automation rate currently standing at 44%.
Production of mechanical parts and engines
In the The Dacia Mechanical and Chassis Plant (UMCD) is also located in the complexone of the most complex mechanical production sites of the Renault Group. The UMCD houses the largest aluminum foundry of the Renault Group, with a capacity of 29,000 tons of parts per year. The aluminum parts, after being melted, are machined to remove excess material, after which they are sent to internal assembly lines or exported to other plants of the Renault Group. The plant also produced engines and gearboxes that equip vehicles of the Dacia range, such as the Sandero Stepway, Logan and Duster, as well as models of the Renault range, including the Clio.
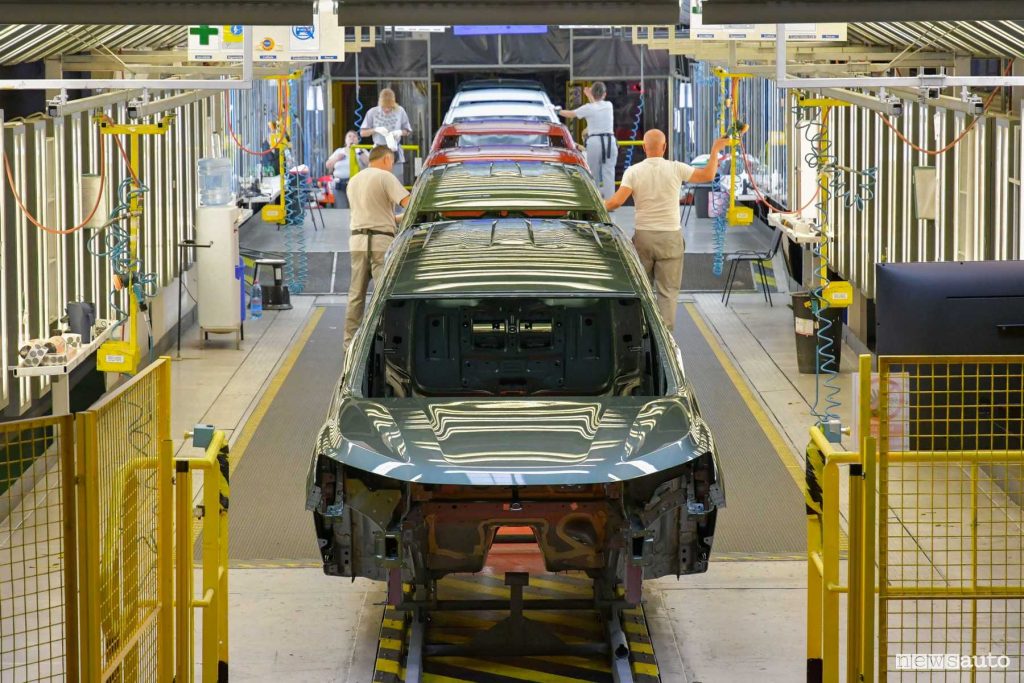
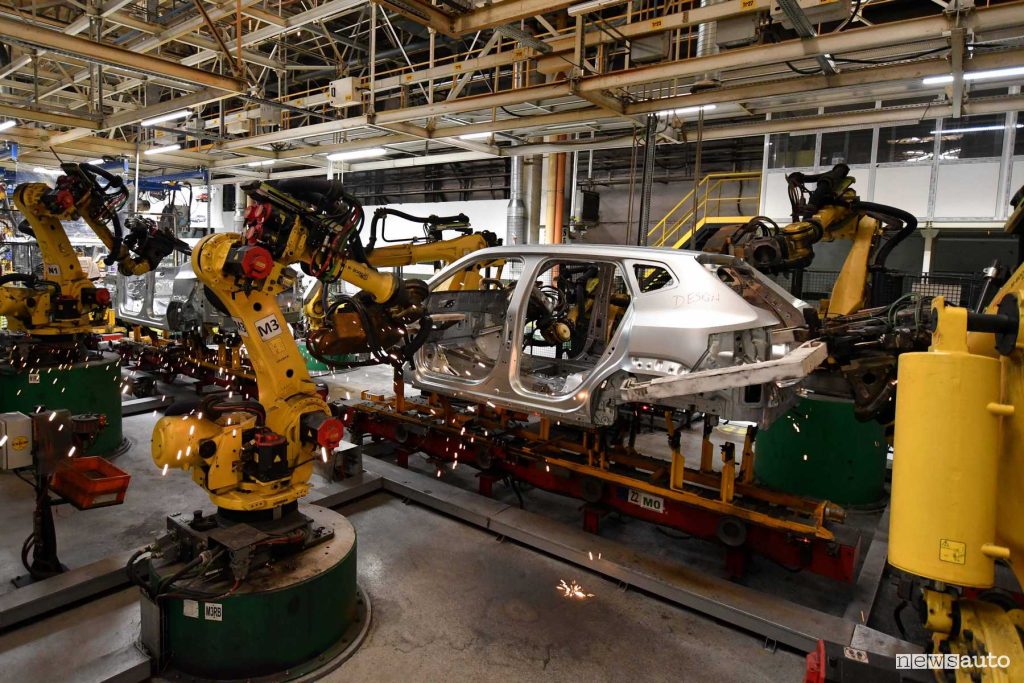
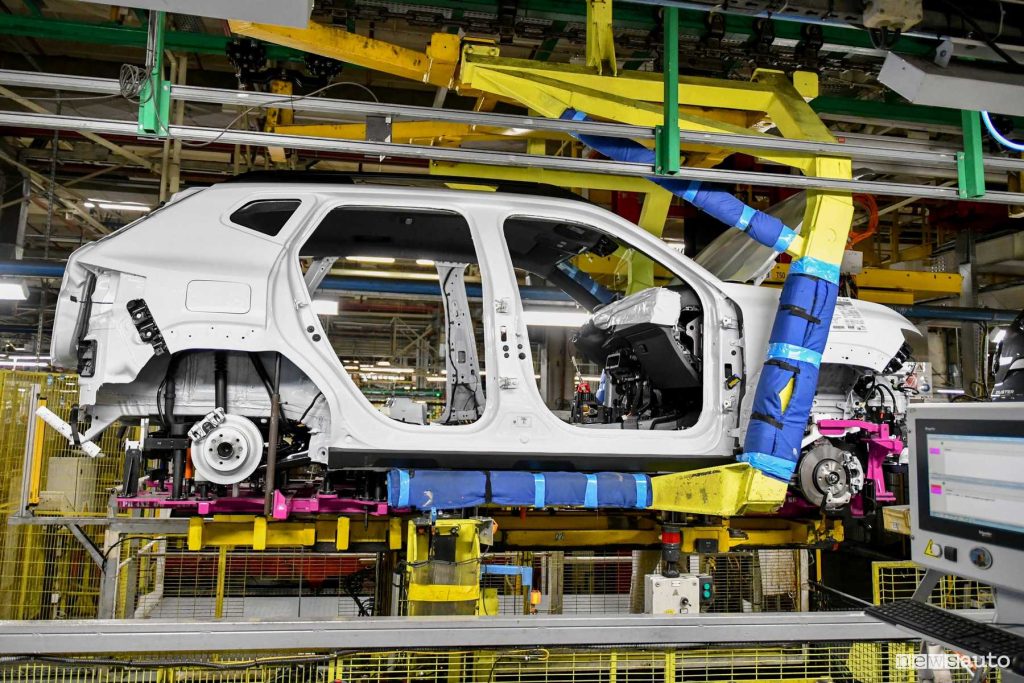
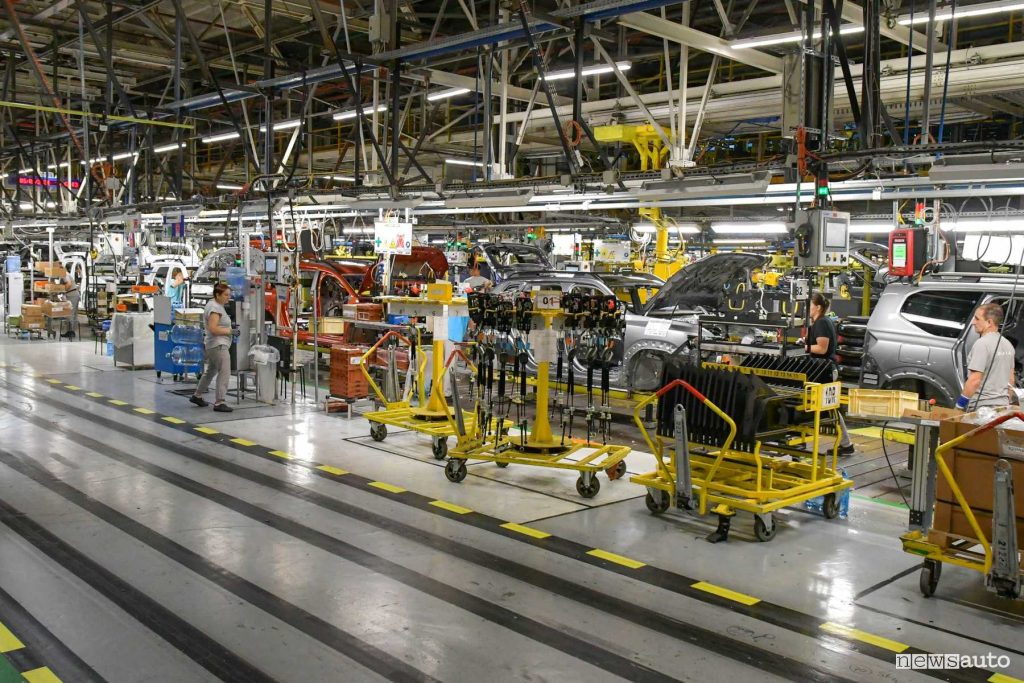
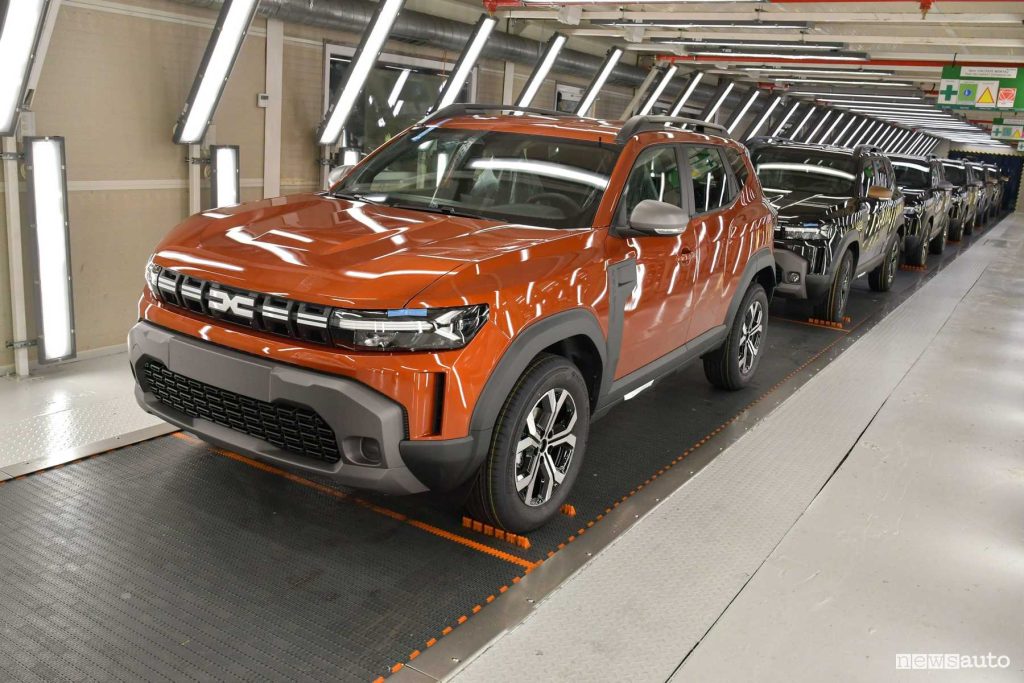
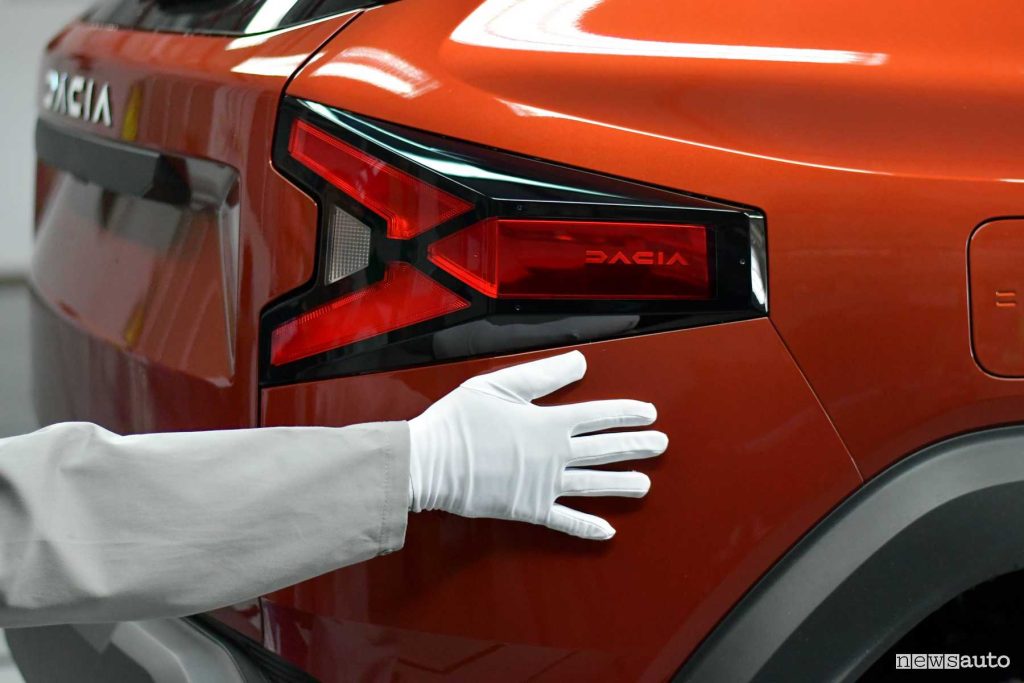
The body shop, for example, is completely automated, with a thousand robots working in the dark to reduce costs and environmental impact.
The production of the new Duster takes place on 468 workstationswith components delivered just in time by autonomous trolleys, ensuring efficiency and precision.
Testing and quality control
Before leaving the plant, each assembled Dacia Duster goes through an hour of quality controlsincluding a water tunnel of eight minutes to check the tightness of the gaskets. The process also includes a driving test on an indoor track to check the functioning of all the components, such as steering, brakes and sensors.
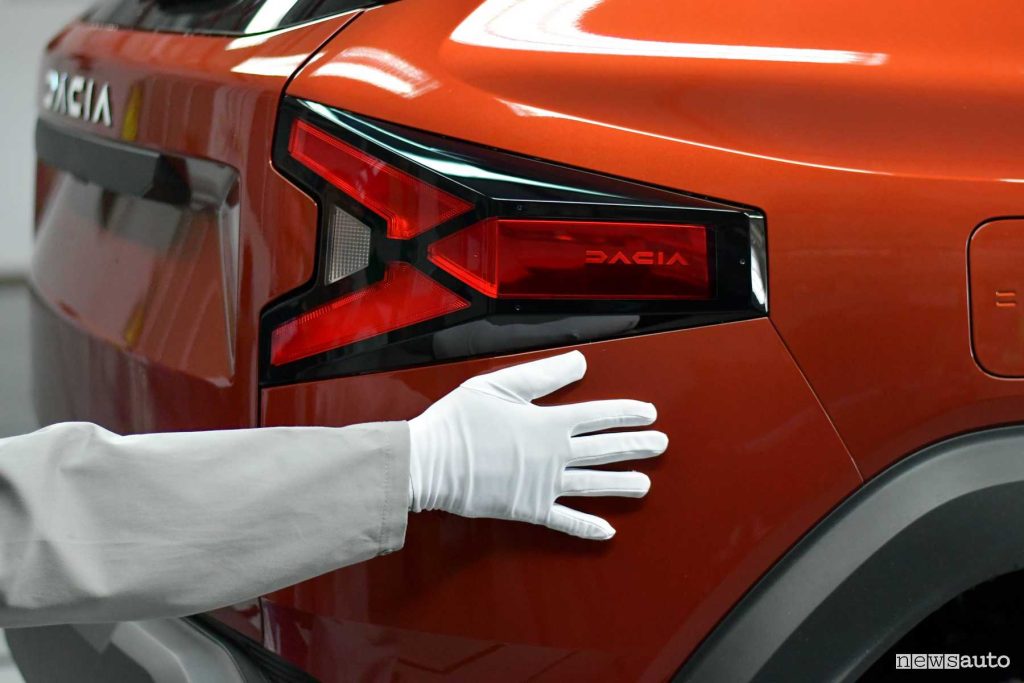
This complex production process, with numerous fundamental steps, guarantees a high quality standard and the best value for money for motorists.
The numbers of the Dacia factory in Romania
EXTENSION | 288 hectares |
DAILY PRODUCTION | 1.400 |
ANNUAL PRODUCTION | 350,000 |
INLINE WORKSTATIONS | 468 |
STAFF | 7,000 |
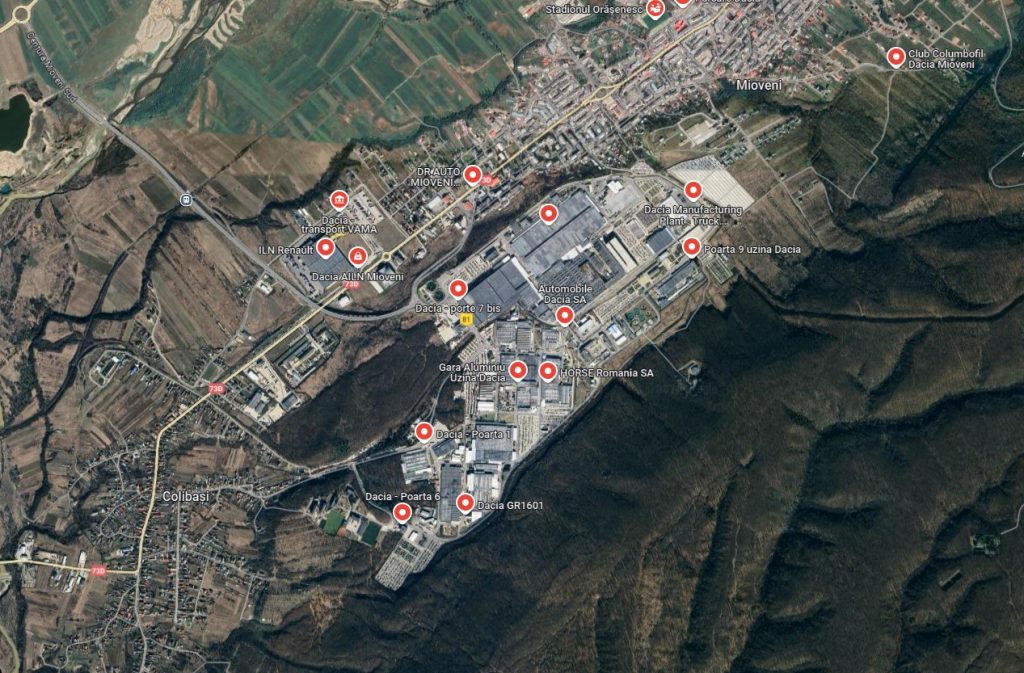
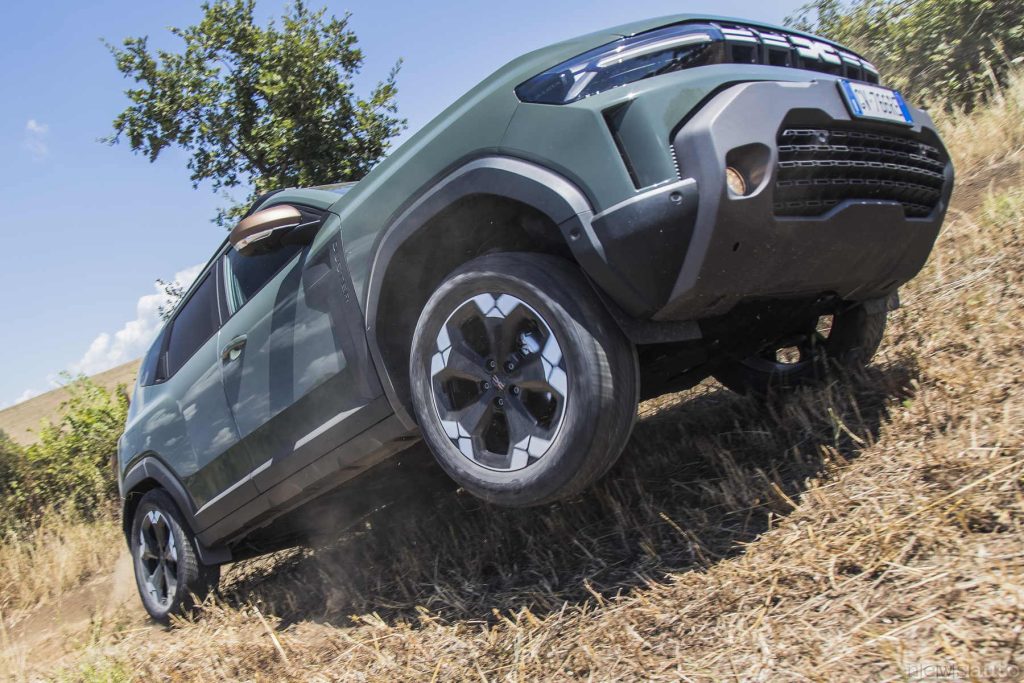
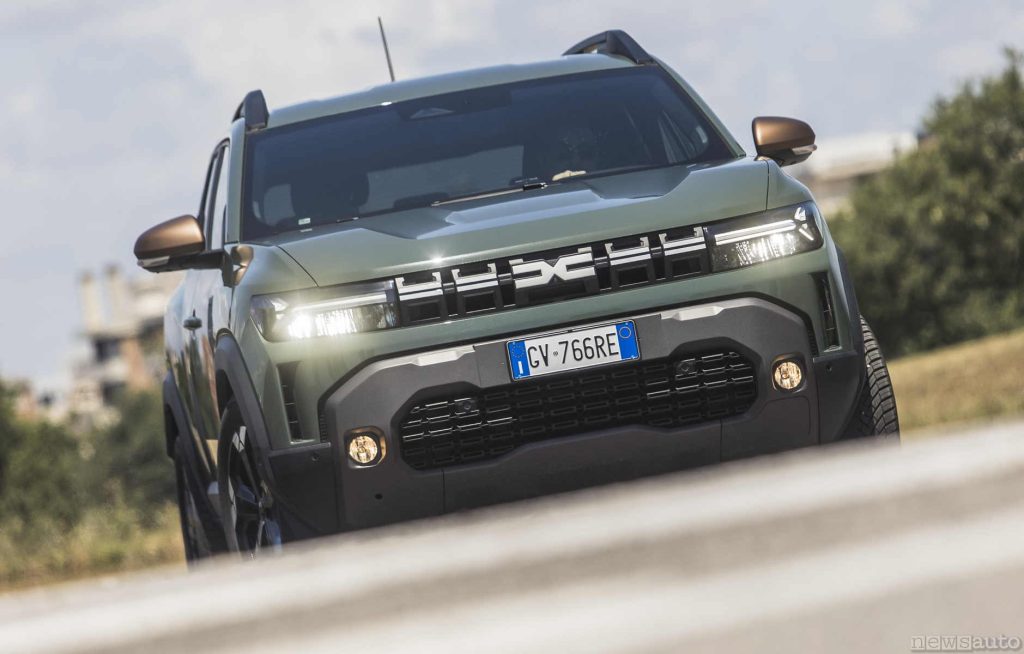
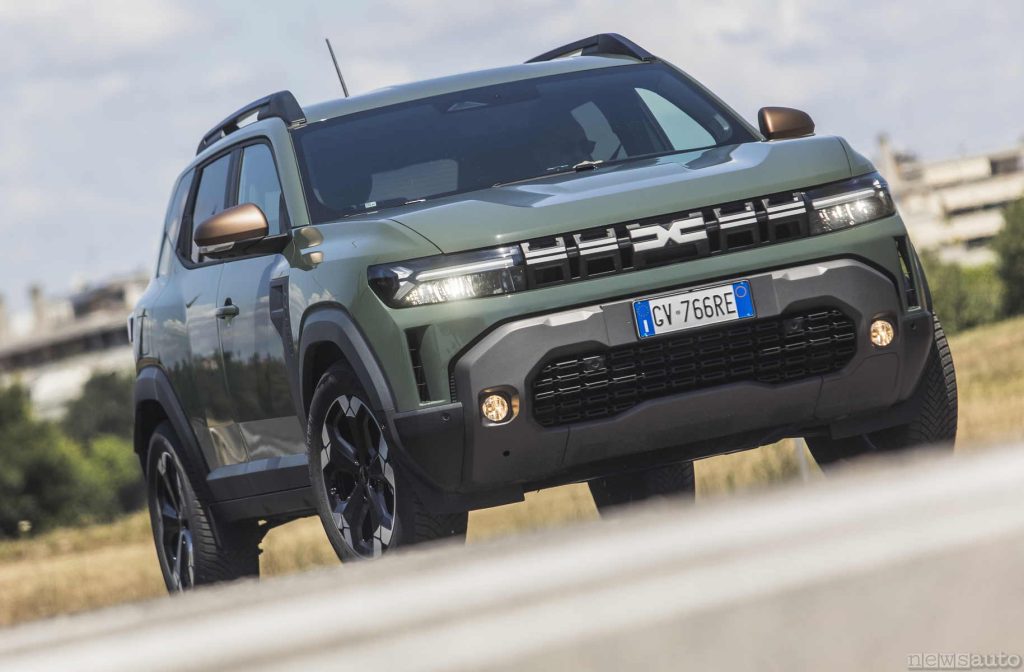
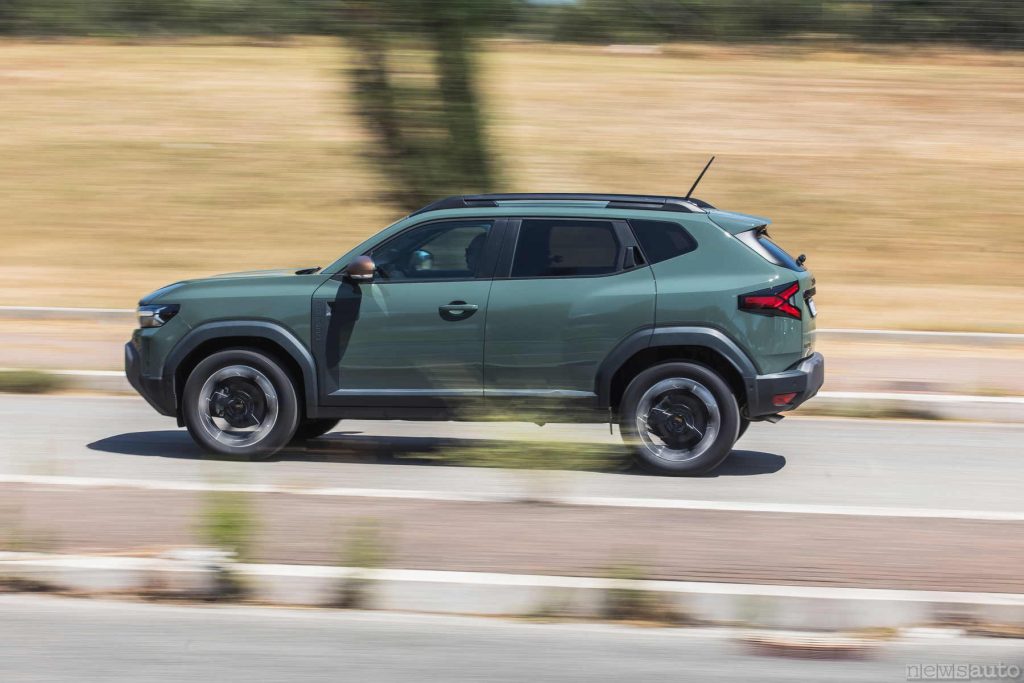
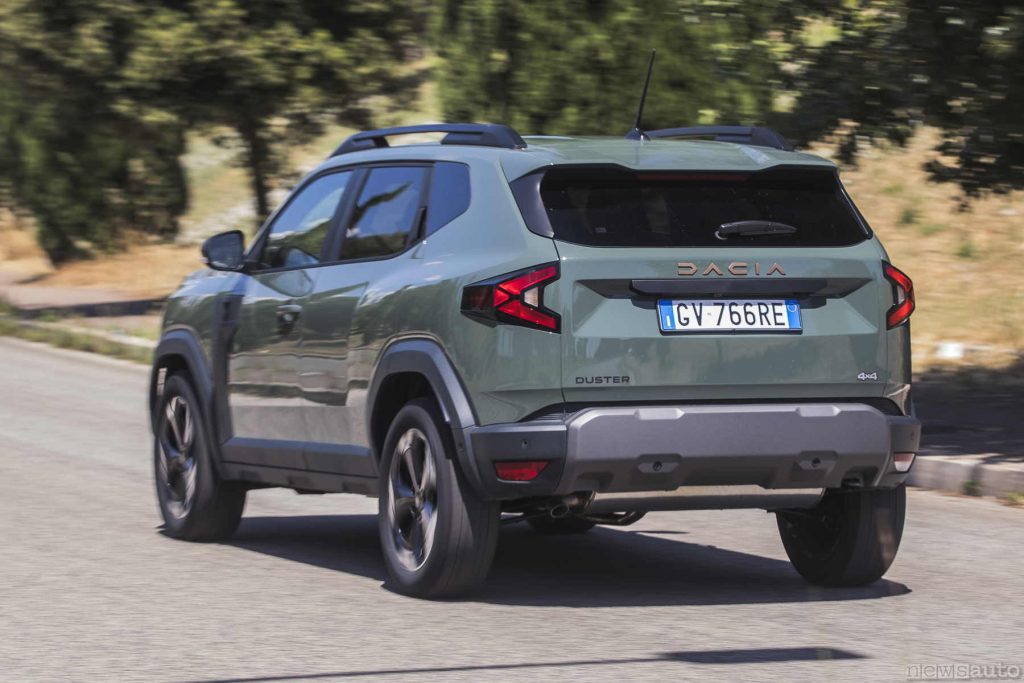
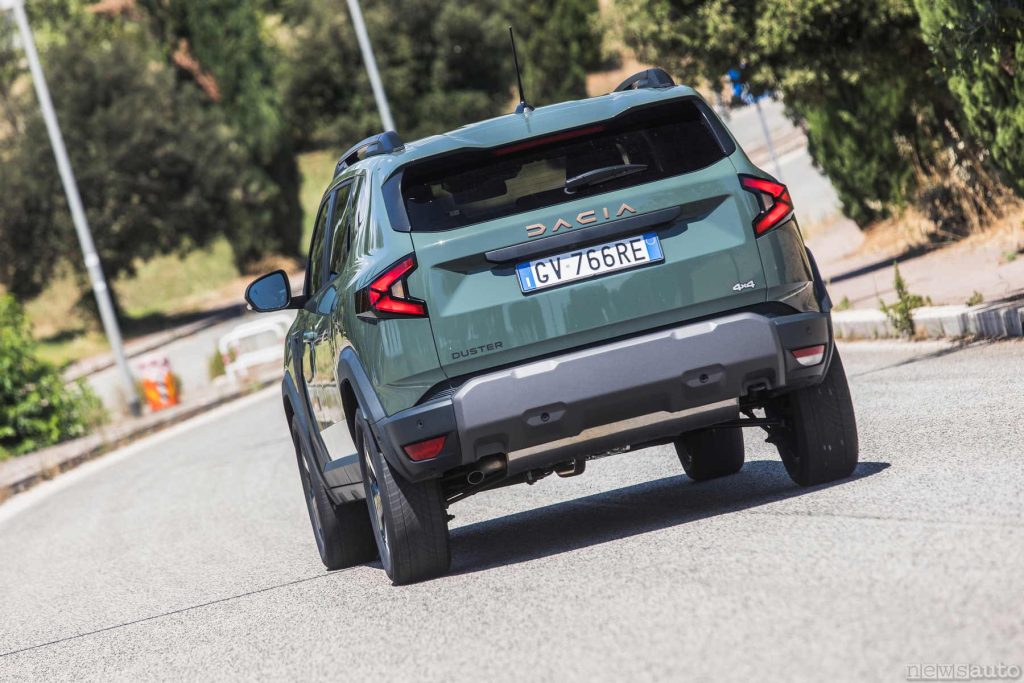
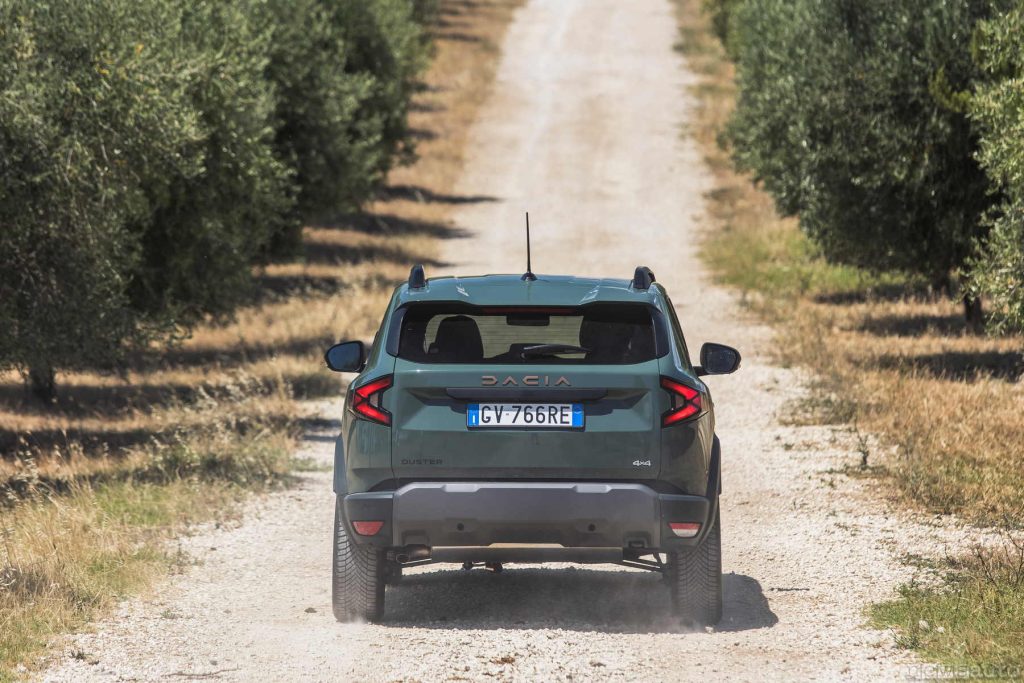
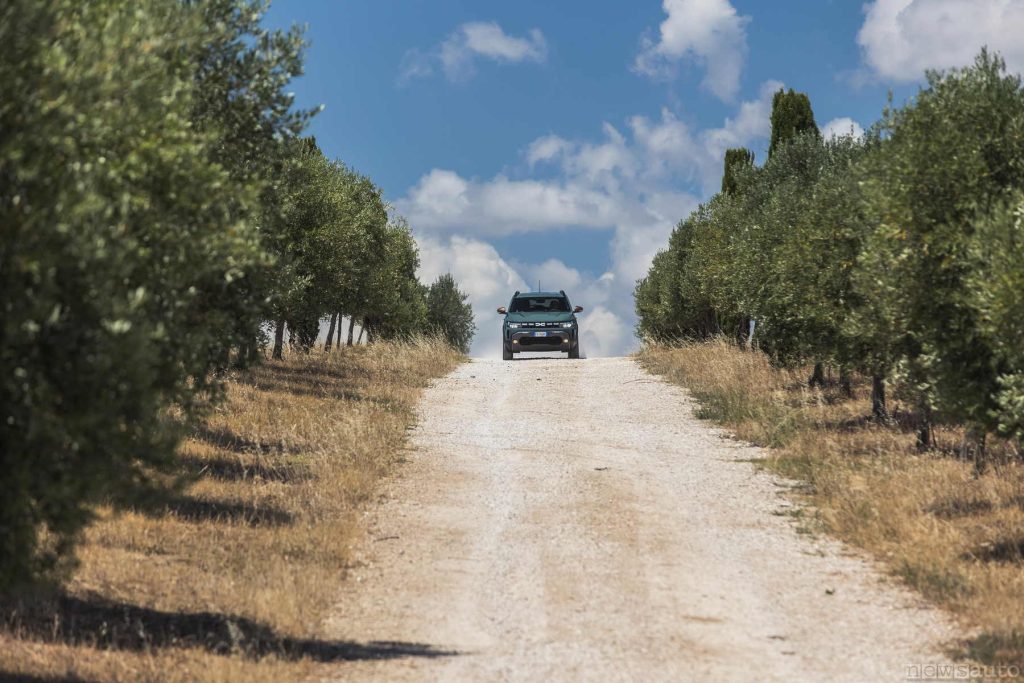
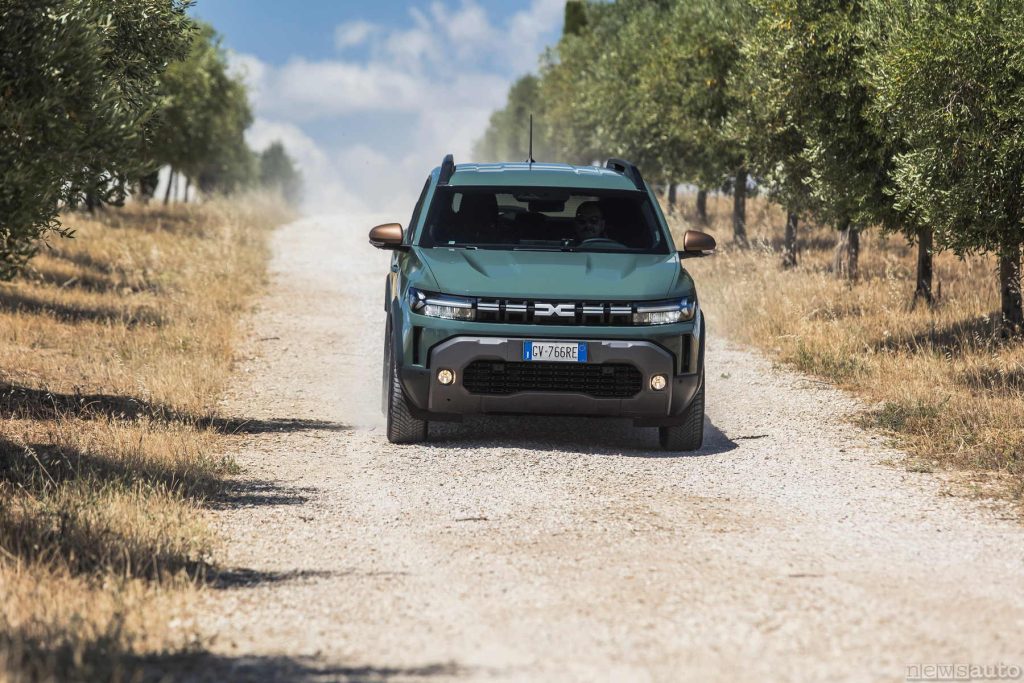
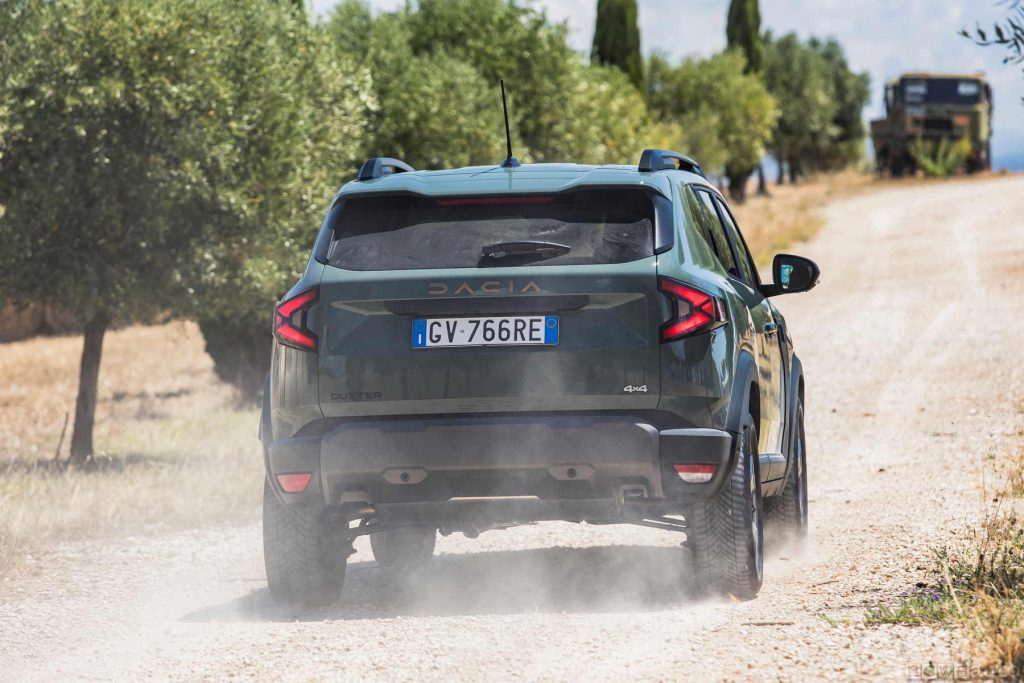
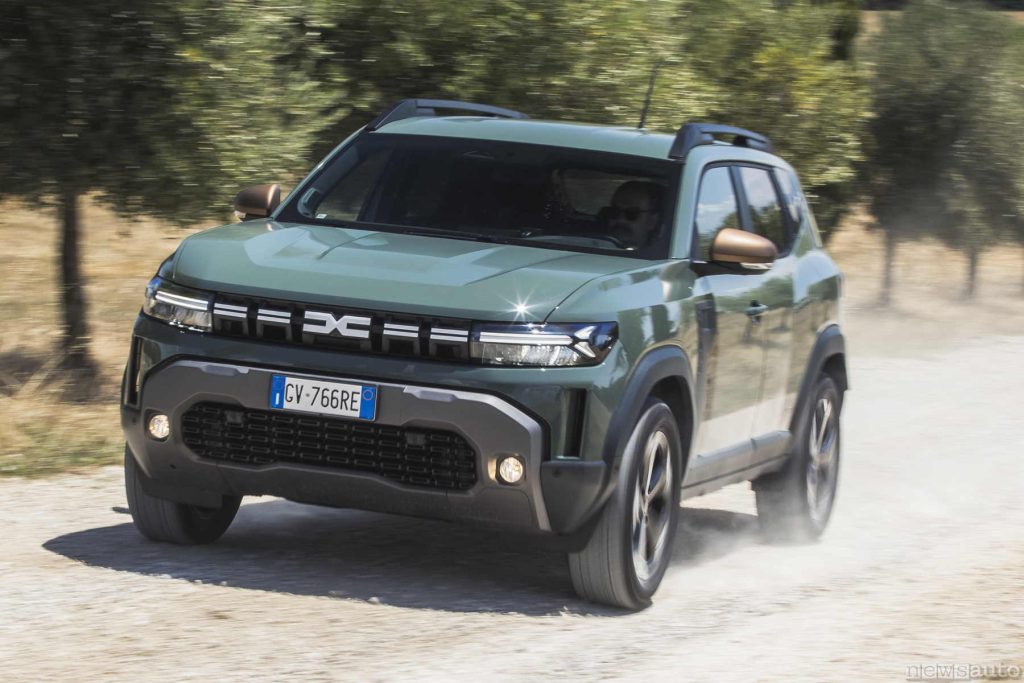
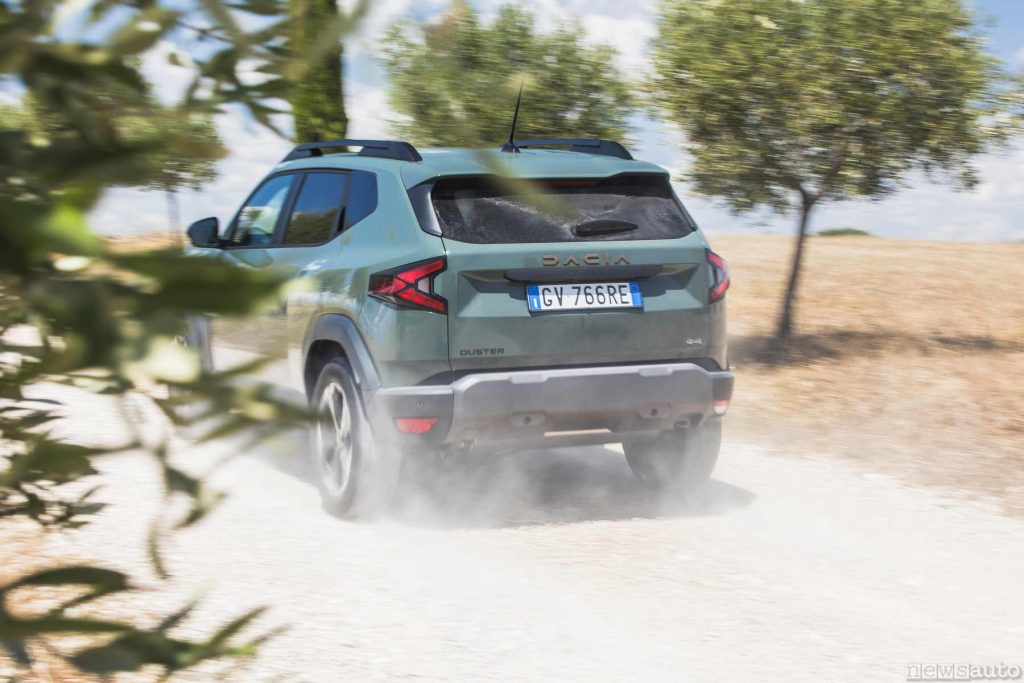

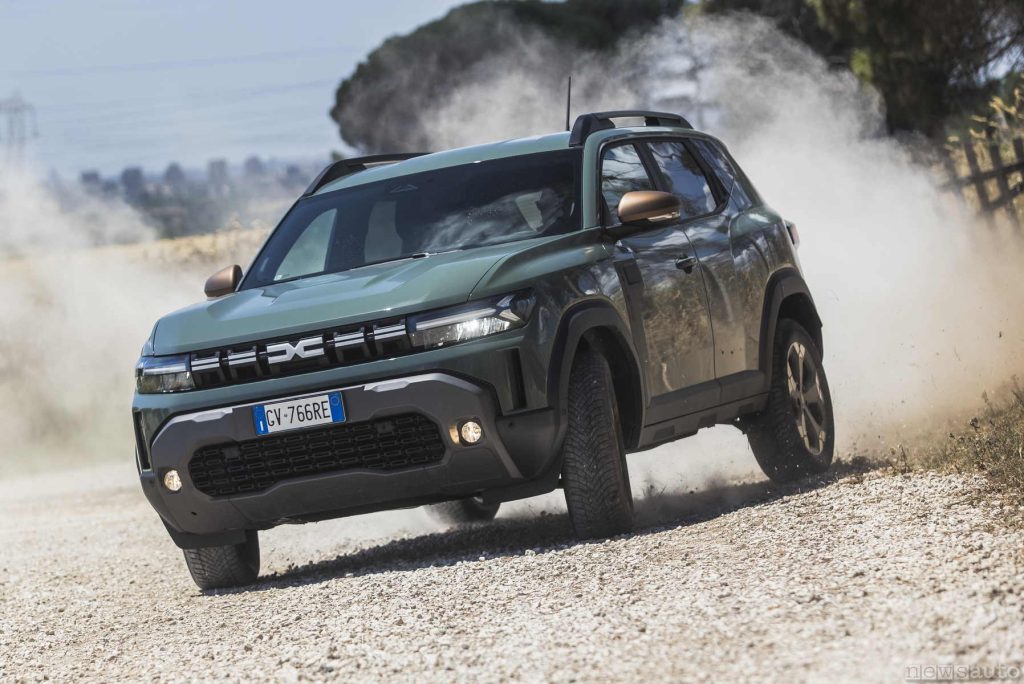
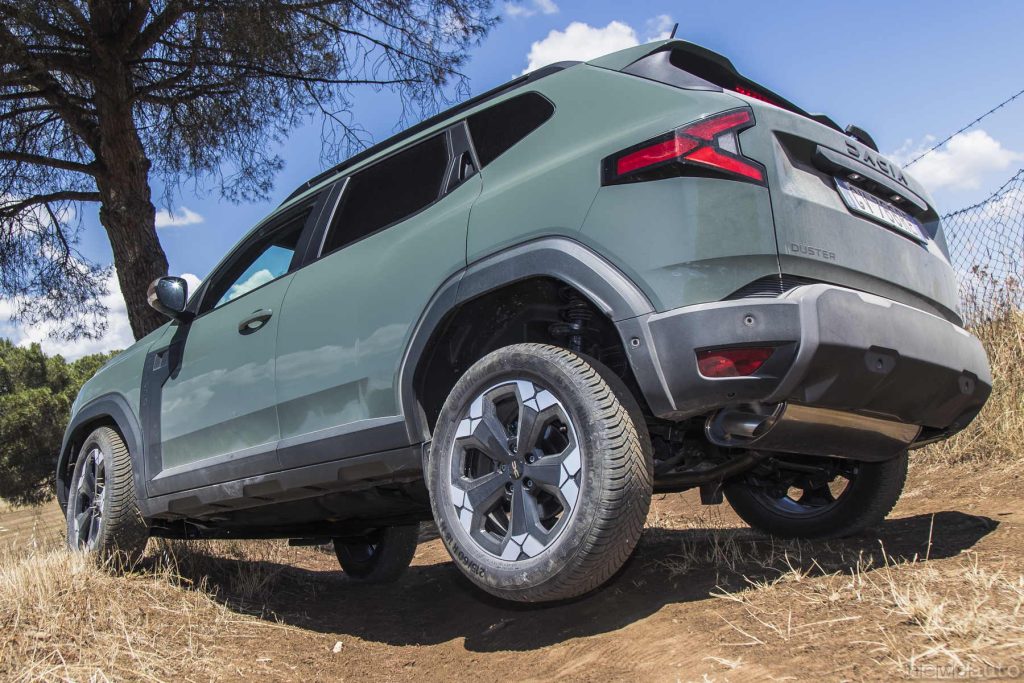
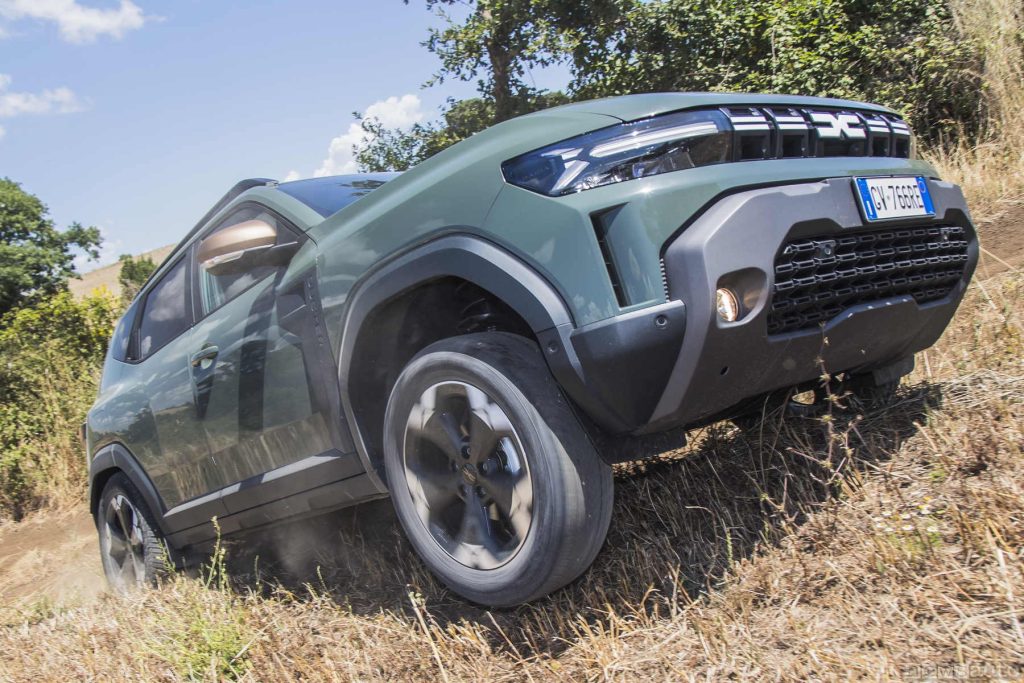
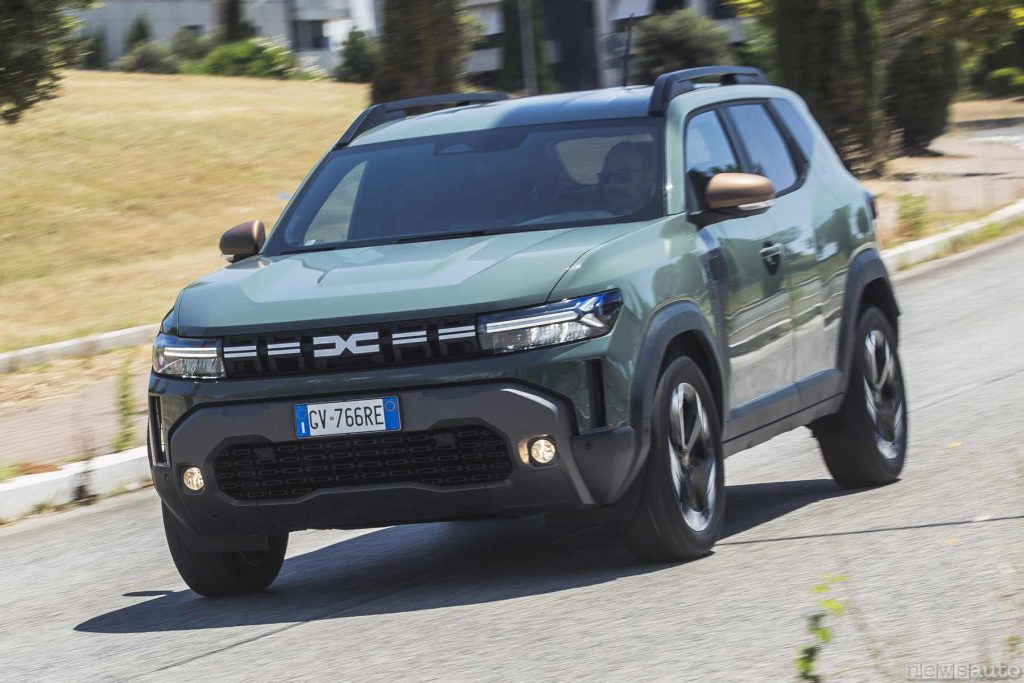
Read also:
→ Test, complete test Dacia Duster 4×4
→ How much does the new one cost? Dacia Duster 2024 PRICES
→ All the articles where we talked about the Duster
→ What do you think? Take a look at the discussions on the FORUM!
#Dacia #Duster #born #technological #factory #Romania