The prosperity of aluminum alloy structural components, including thin-walled design, lightweight, high strength, and strong corrosion resistance, make them widely used in different fields of industrial development. However, the complexity of the internal structure in these parts often leads to challenges during CNC milling processes.

Inaccurate cutting forces have a direct impact on the quality of thin-walled parts, making them susceptible to deformation and less accurate than expected. In addition, thin-walled parts will be subjected to cutting force will lead to deformation, whether the blade is broken and processing the impact of overheating and other factors will also lead to deformation of thin-walled parts and lead to the overall accuracy of the deviation.
The usual approach of machining factories to guarantee the accuracy of CNC milling processes involves non-feed machining multiple times after the final precision machining of thin-walled parts. Although this technique can enhance the quality of thin-walled parts, it leads to a waste of time and resources which is inefficient and unnecessary.
Furthermore, residual fine debris from the tool’s trailing edge in the gaps of the workpiece can cause the surface of the thin-walled parts to become rough.
To address the current challenges faced by factories in machining processes, solving the deformation issues of thin-walled parts during custom CNC milling services and efficiently producing high-quality thin-walled parts have become primary research focuses, particularly in the context of industrial design prototypes.
- Starting with Optimizing Machining Materials
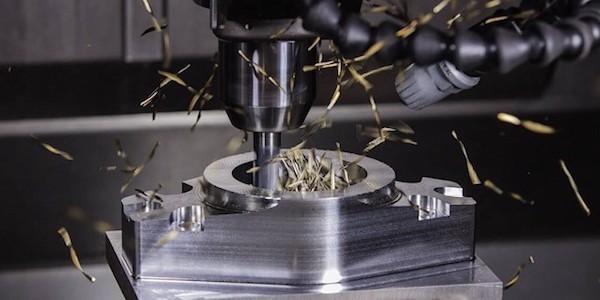
We have noted that special material properties of thin-walled parts cause deformation under clamping and machining heat; hence, we must find a better material for the machinability to avoid this issue— ensuring that thin-walled parts are unaffected by the machining heat as well as clamping process.
To begin with, we can opt for materials that remain intact under machining heat (and thus do not deform) while being machined into thin-walled parts during CNC milling. This choice of materials helps in two ways: it reduces material loss due to deformation during machining heat and also contributes to the production of quality thin-walled parts.
Moreover, given that thin-walled materials find their usage predominantly in high precision demanding fields like aerospace, choosing superior quality material acts as an effective assurance towards the quality of thin-walled components.
2. Improving and Optimizing CNC Milling Processes
Due to the high demand for quality and precision in thin-walled parts within aerospace, we can enhance such elements by fine-tuning the CNC milling process.
The first aspect to focus on is the strict selection of appropriate and high-quality cutting tools. Additionally, selecting suitable cutting parameters is essential. These preparatory steps are crucial because specific machining processes in CNC milling have strict standards.
Poor overall results of thin-walled parts are often due to disarray in the machining process. Therefore, optimization must be carried out on the CNC milling process for typical thin-walled parts— allowing them to find applications in more fields.
3. Setting More Reasonable Cutting Parameters.
The choice of cutting parameters holds a crucial place during CNC milling for thin-walled components. These parameters’ appropriateness directly influences the precision of thin-walled parts— a critical evaluation in industrial design prototyping where post-prototype design tests need to establish strength, tolerance and assembly accuracy among other factors.
Optimal cutting parameters thus help to guarantee that what you intend your design to meet in terms of specifications and manufacturability is upheld. The decision on these rational cutting parameters, therefore, needs careful consideration of different factors and actual conditions as well.
In this case, the parameters include the cutting speed of the end mill, spindle speed, and tool size. All these factors must be analyzed together to guarantee that thin-walled parts produced through CNC milling will have quality standards and be highly precise.
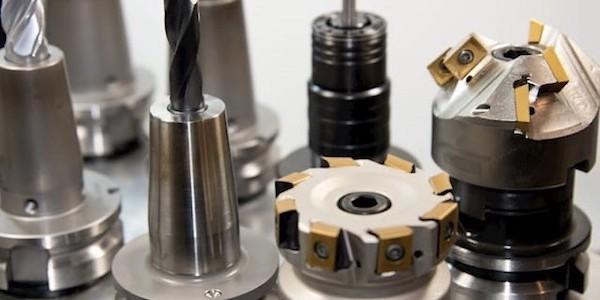
In addition, the choice of cutting parameters can significantly differ based on various machining materials and tool materials. Therefore, it is important to make a selection in a customized way to the situation. This aspect taken into account properly could considerably enhance the quality of thin-walled parts that are demanded with high precision requirements from different fields — which can then promote their wide use — as components in other industries.
4. Developing Appropriate Workpiece Clamping Solutions to Improve Machining Quality
Clamping solution is just as important as choosing the right cutting parameters. It’s one of the reasons why deformation happens when machining thin-walled parts: using an improper clamping solution can easily lead to workpiece deformation under clamping force. Throughout the process, tool cutting might lead to issues like ‘over-cutting’ or ‘under-cutting’; these are typical situations where geometric errors and deformations manifest on the workpiece surface— which consequently compromises machining quality. When dealing with a thin-walled structure that lacks rigidity, note that inappropriate clamping greatly contributes to workpiece deformation.
Clamping solution should be considered for thin-walled parts— as it relates to precision, surface quality, production efficiency and cost in CNC milling. The primary concern when devising a clamping solution for thin-walled parts is to consider the structural features of the parts together with the technical requirements of the machining process. In order to determine the areas likely to be deformed, detailed analysis and calculation of specific data should be carried out. Structural feasibility plus practical implementation are two main issues to address in developing a clamping solution for thin-walled parts.
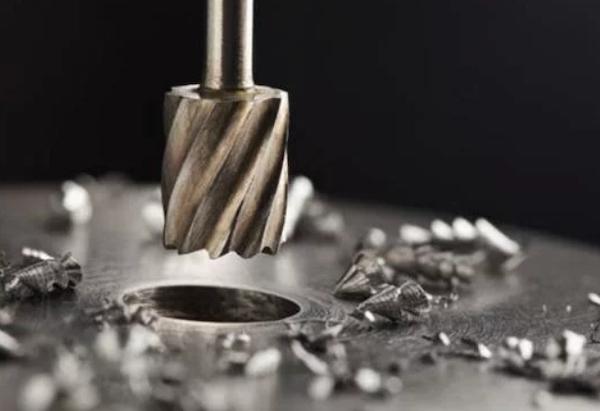
Furthermore, selection of positioning and clamping force are critical factors, as well as the clamping approach. This guarantees that the workpiece is exposed to least amount of force and torque— thereby thwarting any harm while attaining optimal thin-walled part precision.
Conclusion
Thin-walled parts are being used more commonly now in various fields, including aerospace engineering. As a result, the quality demands for these machined thin-walled parts have soared. CNC milling is a primary technique for producing these thin-walled parts; hence, continuous enhancement and fine-tuning of the CNC milling process should be made to make improvements on the quality of those parts. This paper puts forth some conditions and proposals on how to better the quality of thin-walled parts when going through the CNC milling process with the objective of reforming associated procedures.