F1's hope is to one day eliminate aerodynamic development in the wind tunnel, with the aim of further reducing costs with research carried out only virtually with CFD systems. Computational or numerical fluid dynamics (the English acronym derives from Computational Fluid Dynamics) is a method that uses numerical analysis, algorithms and recently also artificial intelligence to solve and analyze fluid dynamics problems through the use of computers with ever-increasing computing capabilities.
Photo by: Sutton Images
Nick Wirth, Simtek Team Principal, with Max Mosley, FIA President in 1994
Nick Wirth was the first to believe in the design of a single-seater without wind tunnels at the beginning of the '90s, but the birth of Simtek at CFD was certainly not a virtuous example. Simulation systems have made extraordinary leaps forward and the function of the wind tunnel has changed radically due to the enormous costs it requires. Once upon a time, F1 teams mounted all the modifications they thought of on the scale model and only after a selection were they chosen the parts that gave the best results, giving life to the upgrade packages.
The aerodynamic evolution of a single-seater was rather slow, because the scale detail, once approved in the gallery, was made in full size and produced to be mounted on the car. Today the screening takes place with the CFD study, while the approval of the approved changes takes place with a check in the wind tunnel.
The model makers, extraordinary craftsmen who knew how to create the elements of the bodywork or wings with wooden or fiberglass parts, have seen their work change drastically: in F1, 60% scale models made of carbon fiber are used which must reproduce the characteristics of real cars, supporting in proportion the loads to which the car is subjected on the track.
With the introduction of 3D printers we have witnessed an acceleration of development times, because parts in composite materials that had to be laminated and then cooked in an autoclave can now be created with rapid prototyping, which allows you to create a piece starting from from a digital three-dimensional model thanks to a CAD file.
Automation is total because it has replaced the artisanal production of the prototype: 3D printers, thanks to additive technologies of powders, filaments or resins, are able to define very complex parts that would be impossible to obtain with traditional techniques by removal from a single block of material .
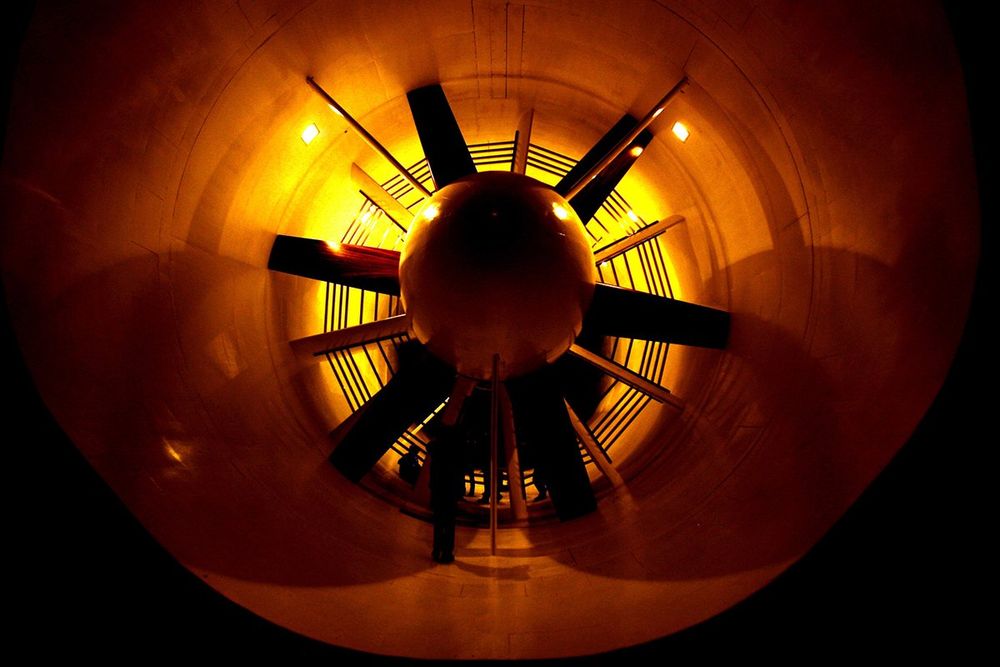
Photo by: Red Bull Content Pool
Here is the Red Bull wind tunnel fan in Milton Keynes
The evolution of materials has led to increasingly sophisticated aerodynamic research, capable of ever more faithfully reproducing the data that is then read on the track (the famous correlation that all teams look for). The investigation once envisaged that the model would be hit by the air flow of the fan only from the front with a maximum speed of 50 m/s, equal to 180 km/h, while more recently the behavior of the car in yaw has also been studied, that is to say with the wheels turned, as if it were on a curve.
The wheels which were made of wood have rims and tires produced by the sole supplier. The first to introduce WTT (Wind Tunnel Tyres) was Bridgestone at the time of Ferrari's domination in the Schumacher era, but Pirelli then carried out careful development work which allowed it to design and build “tyres” with the same profile of the tires used in GPs and with increasingly likely shoulder deformation characteristics.
It may seem incredible, but at Pirelli there is a small staff dedicated to the evolution of the WTT which follows the changes in the 18-inch tires in parallel. The only thing that is substantially different is the compound: in the wind tunnel none of the five compounds approved for one season are used, but a special specification (usually harder) is approved.
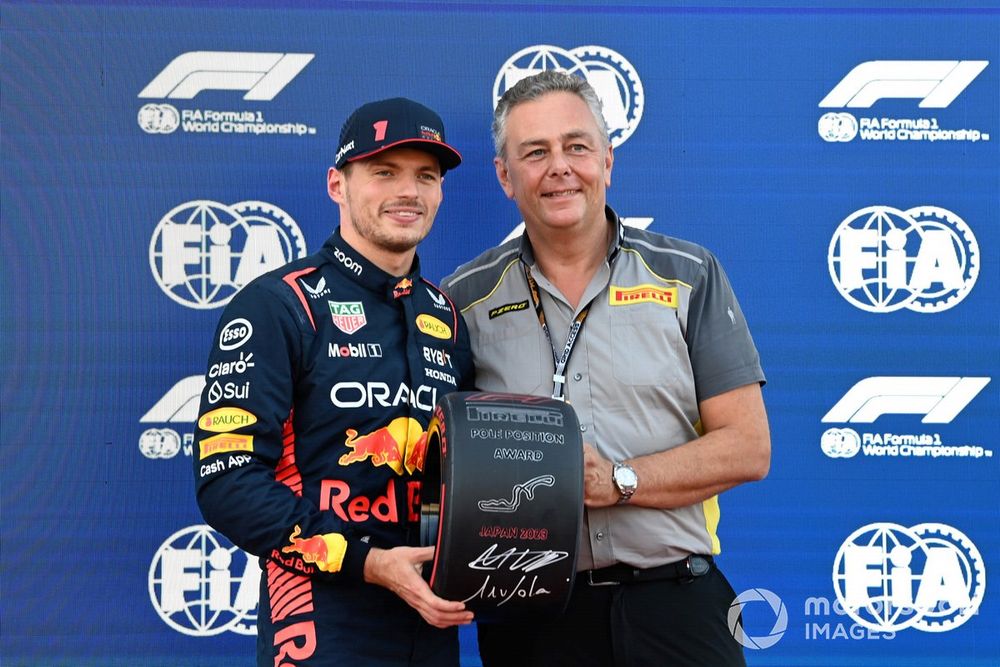
Photo by: Mark Sutton / Motorsport Images
Verstappen receives the Pirelli Pole Position Award from Isola which is equal to the tires the teams receive to use in the tunnel
Since the wake of the front wheel strongly influences the aerodynamics of a modern F1, the teams have paid greater attention to the rubber. Each team receives 12 sets per season from Pirelli (the 2023 ones must be returned to the supplier by February 28) and they must be enough for the entire championship.
It is emerging that all wind tunnels are constantly evolving: the moving walkway on which the wheels rest was a metal matrix strip capable of reaching the same speed as the air flow, while a sophisticated suspension mechanism allows the model to simulate all the maneuvers that an F1 car performs on the track: acceleration and braking, yaw and even drifting.
The mesh of the metal matrix has become increasingly finer, but more recently the carpet has been covered with a rubber skin. The need was to reduce the friction of the WTTs in yaw, also controlling their consumption. And so, the research pushed the teams to develop plastic film layers that can even reproduce the roughness of asphalt.
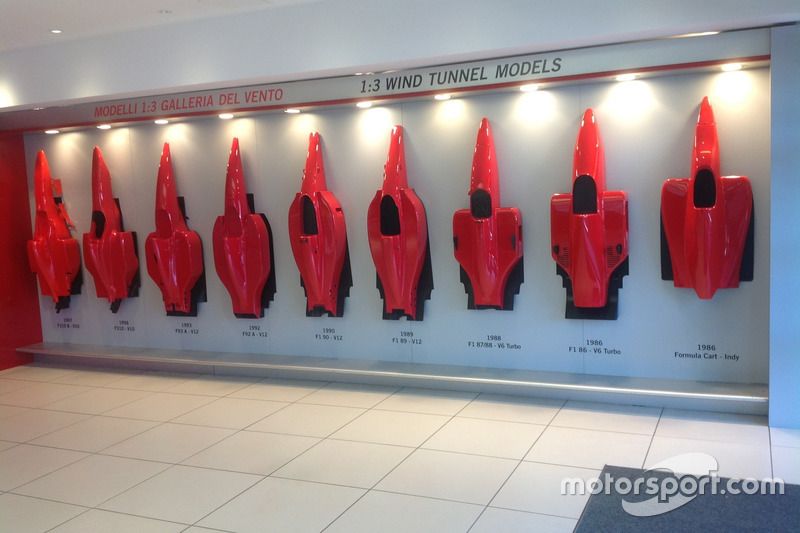
Photo by: Franco Nugnes
Ferrari: some 1:3 scale wind tunnel models exhibited at the Maranello Museum
The FIA, in the hope of bringing together the performances of the top teams with those of the customer teams, has imposed severe constraints on wind tunnel research, penalizing the richest and most competitive teams: world champion Red Bull can have 605 hours in the top six months, compared to 720 for Mercedes and 768 for Ferrari. There are no huge differences between the top three in the Constructors' World Championship, while the gap opens up going down the ranking: the last Haas can count on 1,108 hours, while AlphaTauri, Red Bull's junior team, can reach 1,008.
The numbers say and do not say, because it is becoming increasingly clear that in tunnels the quality and efficiency of the investigation always counts more than the number of hours granted. And, then, contradictions can emerge: is there a greater advantage in using fresher WTT tires with fewer hours available like Red Bull, or by spreading them gradually over the course of the season?
We are entering increasingly extreme areas of specialization: there are teams, in fact, that are also paying particular attention to tire inflation pressure. We have gone from metal or wooden wheels to the study of pressures. And certain research has intensified with the ground effect single-seaters introduced in 2022.
By now we have all understood how important it is to keep the bottom of the single-seater as close as possible to the asphalt to generate aerodynamic load: the teams that still have a tunnel with the metal matrix moving walkway cannot go too low, because if the model were to rubbing on the floor could destroy it, with serious damage to materials and development times. Those who, however, have been able to adapt the carpet with plastic films, could dare to go lower with the bottom.
It emerges, therefore, how the growth of an F1 is not only related to the ideas of the chief designer, but also to the ability to adapt the structures and tools available with an evolutionary work that never stops. But at this point a question arises spontaneously: whether Red Bull, which uses the same tunnel as AlphaTauri in Milton Keynes (but Ferrari could equally do so with Haas, rather than Mercedes – for a little while longer – with Aston Martin) were to assign the tire pressure tests to the team led by Laurent Mekies, the world champion team could benefit from the results without spending a minute of its precious gallery time.
In the depths of the budget cap there are many ways to optimize costs and this is an example that can explain why the advantage would fall on both teams…
#Incredible #tire #pressure #studied #tunnel