After difficult years, especially on a financial level, step by step Williams seems to see the light at the end of the tunnel, even if the goal is still distant. Thanks to the arrival of Dorilton Capital, the team was able to access new investments with which to strengthen not only the staff, but also the structures.
In fact, it is no mystery that, beyond the organizational and human shortcomings, Williams also had to deal with equipment that was long out of date and in some aspects was years older than its rivals. A state of decline resulting from the poor investments made before the private company entered the group, which allowed the release of funds that were impossible to reach under the previous ownership.
One of the fundamental steps was to entrust the leadership of the team to James Vowles, an engineer with long experience in Formula 1, not only thanks to his long career in motorsport, but also thanks to the years spent in a leading role in Mercedes' winning cycle . His figure was considered the most suitable to guide the new course, also thanks to his human qualities, which made him become a real reference within the team, not only from a technical and organizational point of view .
Alex Albon, Williams FW46
Photo by: Zak Mauger / Motorsport Images
Furthermore, the arrival of Vowles, as well as the large investment program undertaken by Dorilton Capital, has allowed it to attract other engineers from rival teams, such as Pat Fry, who left Alpine last year to embrace the new project of the Grove house.
The seventh place achieved last year, although achieved also thanks to specific characteristics of the car, immediately represented a sign of the ambitions of the team, which no longer wants to be the leader of anything, but rather a team with ambitions. To achieve this, however, first of all it was also necessary to review the organizational processes and structures, which in the past have cost Williams both time and money. Sometimes the cost of new equipment can be amortized with greater efficiency within the company, as in this case.
“From the second day I arrived at Williams, I immediately understood that it would be a difficult journey. There was very little compared to what I was used to,” said James Vowles, addressing the comparison with Mercedes and what steps Williams needed to build the first foundations.
“It didn't take long before I realized there was very little compared to what I was used to. And I don't just mean in terms of structures and buildings. But about processing data. There wasn't even data on the cost of a component! There was also no data on how long it took to produce the parts. Or how many components were present in the system to be built. When this data is missing, it is difficult to understand how difficult it was to manage a car with 20 thousand parts, where they are located in the company, how they will come together, how long it will take to rebuild and develop them”, then added the Team Principal, who already in the early interviews had mentioned how a parts management system was missing.
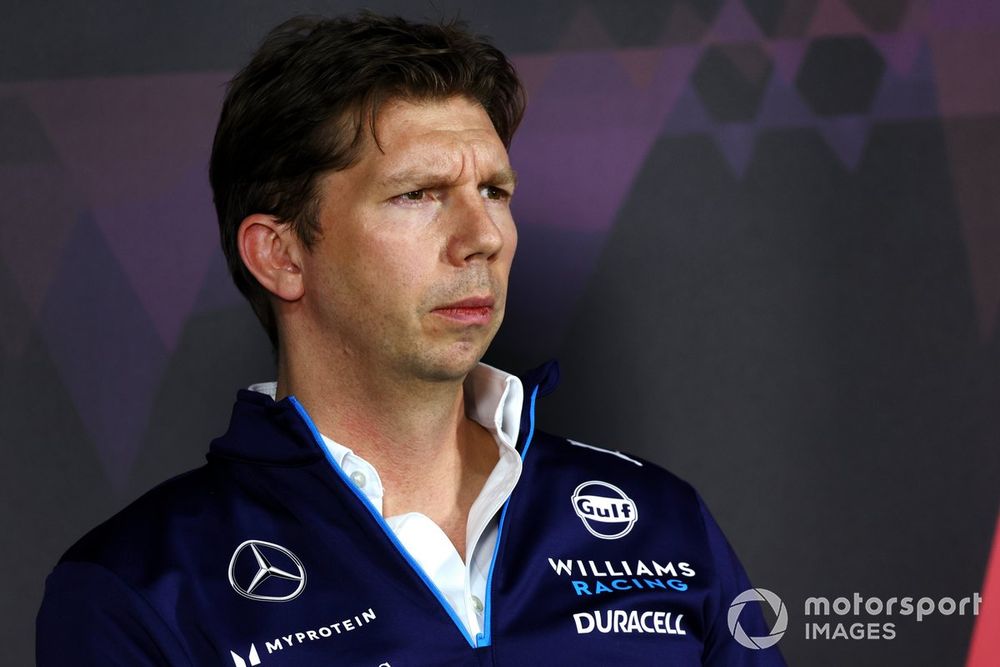
James Vowles, Team Principal, Williams Racing
Picture of: Motorsport Images
One of the first aspects that Vowles worked on was to create a new structure for managing components, so that it was easier to organize the team and the work of the staff. As hard as it is to believe, before his arrival, in fact, all the parts of the single-seaters were managed with an Excel sheet: “The car, as I saw it 12 months ago, was a list Excel. Now think… That's 20,000 components. The list Excel it was a joke. I mean, it's impossible to navigate through it to figure out what you need. And then it was impossible to update. But this is the way the car was built before I arrived,” Vowles said.
This represents a problem not only in terms of organization, but also of cost management, because a team must always be well aware of the wear of a certain component, where it is in its life cycle and whether it is necessary to manufacture more with different characteristics. Aspects that clearly have an influence on the budget, which for Williams is certainly not infinite.
“Let's take the front wing. A front wing consists of approximately 400 pieces. When you say, “I would like a front wing,” you need to put the metal pieces, the carbon pieces that make up the front wing, into the system. And they must be tidy. Is a front wing more important than a front arm? In this case, where do they go? Where are they inspecting? When you start tracing hundreds of thousands of components, move across a sheet Excel It's useless. You need to know where each of those individual components is located. How long will it take for it to be completed, how long will it take for it to go for inspection.”
When it comes to having to manage so many components, it is clear that no matter how much a team can be divided into sectors, it only creates confusion. The exchanges cannot be just verbal, as the various movements must be traced, which is why in the end there was a large exchange of emails between departments which only slowed down the engineers in their search for information.
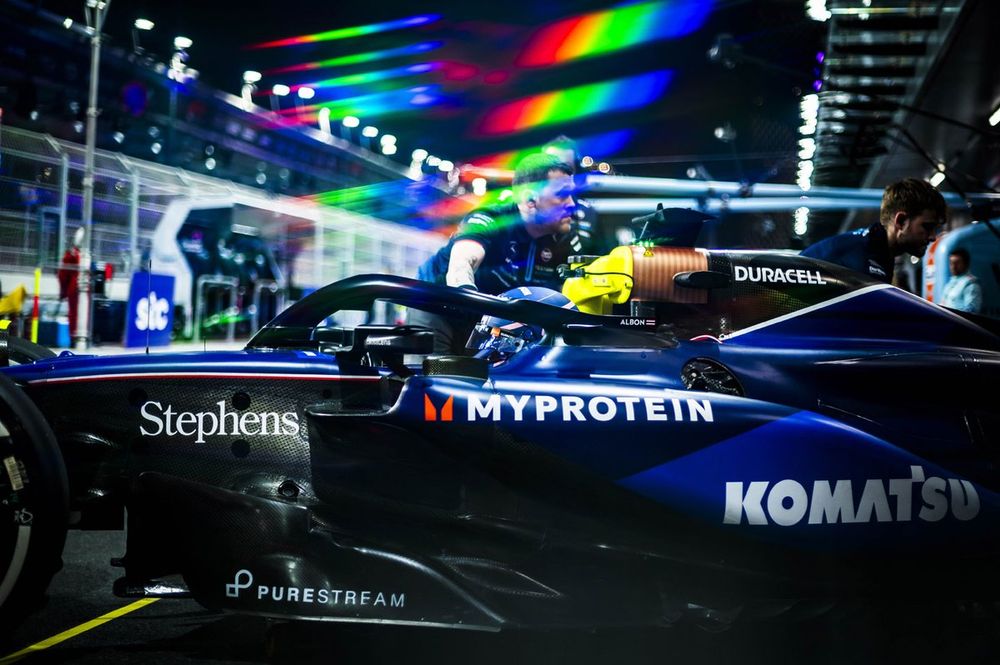
Alex Albon, Williams Racing FW46
Photo by: Shameem Fahath
“It had gotten to the point where the factory was saying, 'I don't know where this component is.' And people often spent time walking around the factory trying to find a component. I wish it was a joke, but it's not. But it gives you an idea of the opportunities we have. Because once you get over this problem and stop worrying about where the individual pieces are.”
Vowles, in fact, pushed for the introduction of a new component management system, something common in other teams, but which represented a small revolution for Williams. On the other hand, however, this process took time, not only for the necessary integration phase within the company, but also because the staff had to adapt to a new system.
“Let's give an example. Our frame went from a few hundred pieces to a few thousand components. This is a very important leap. And at the same time we have a system that has been migrated from a sheet Excel to a digital system. We have therefore changed the way things are recorded and stored digitally within the company.”
However, Vowles' work was not only limited to the organizational and management part, but also to other aspects related to performance. In fact, upon arriving at Williams, the new Team Principal discovered that some parts of the 2023 car had been taken from the 2022 single-seater, but modified in some aspects in order to save money. Although it is true that some elements are recovered from one year to the next, even if they tend to be secondary things, this was an almost common process in the Williams household.
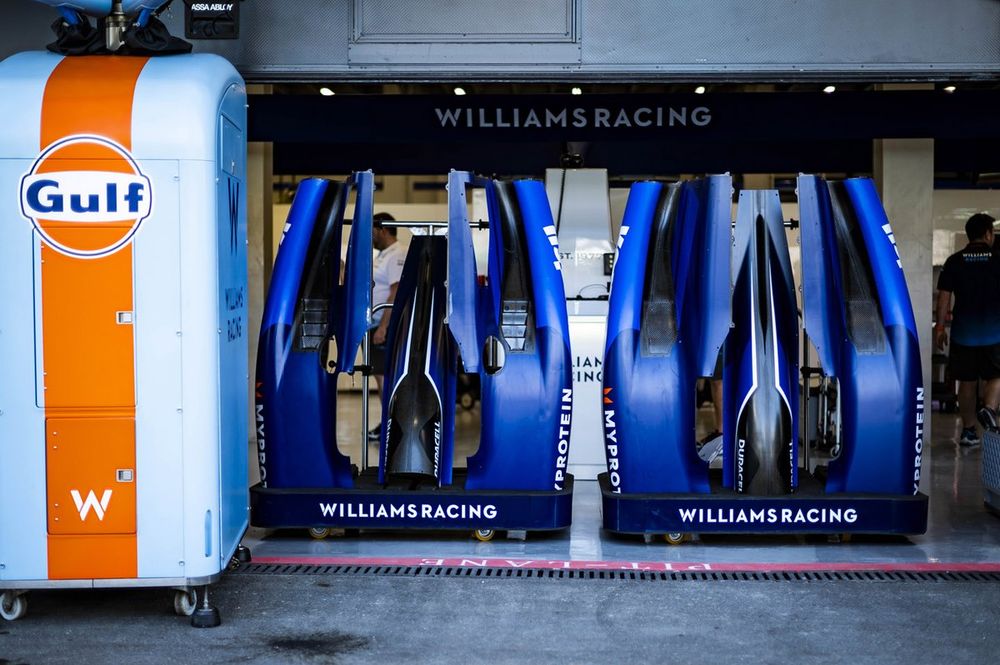
Box Williams Racing
Photo by: Shameem Fahath
Furthermore, some elements of the car were not made of carbon, like the other teams, but were still made of metal, which entails a significant addition of weight if applied to multiple pieces.
“When I arrived, I discovered that some pieces were not made of carbon and were made of metal. If you go back to last year's parts, some of the FW45 was actually made up of parts from the FW44 [la monoposto 2022] at the beginning of last season, because those were the pieces available. So, they would reorganize and change,” Vowles said, explaining why in some cases this was a waste of time.
“These are the unexpected events, the waste, because you spend… it doesn't seem like a lot, but 20-40 hours of design work and then production to get the parts out the door, and none of that is spent making the faster car, actually you make it slower”.
#Vowles #Williams #managed #cars #Excel