By Carlo Platella
Winter is the period in which work on the new single-seaters is completed. Among the many points on the agenda, each team must undergo chassis homologation tests, already passed by Ferrari, which, although known as crash tests, are in reality much more complex. The regulation prescribes dozens of different checks, which can be classified into three categories: impact tests, static loads and design demonstrations. In some cases, in fact, compliance with safety criteria is not verified through physical tests, but rather through calculations and computer structural simulations. Furthermore, the various tests do not concern the single-seater in its entirety, but aim to verify the individual structures from which it is composed. Here is a guide to the main tests.
Security cell
The safety cell constitutes the nucleus of every single-seater, the cockpit in which the driver sits and, therefore, must guarantee maximum safety. The first crash test is that offrontal impact, where the frame is fixed to a trolley using the engine anchor points. In the same structure there is also the fuel tank, filled with water for the occasion, and a dummy weighing 75 kg. The overall mass is 900 kg, approximately equivalent to that of a single-seater in race configuration. The trolley is crashed at a minimum speed of 54 km/h against a wall from which seven horizontal circular carbon fiber tubes protrude, capable of resisting with a resistance force of 50 tons. The test is passed if after the impact no damage is observed to the safety cell, seat belt anchorage points and fire extinguishers. The peak deceleration of the cell must be at least 52 g, but during the test the maximum deceleration at the level of the dummy's chest is also measured.
There are then a series of static tests to be performed on all frames intended for use. In a first test, a load is applied to the side of the safety cell in correspondence with the tank, equivalent to 5 tons and directed inwards, with a maximum deformation of 1 mm after 1 minute of application. Another test, however, simulates the scenario of front suspension failure, when normally the wheel hits violently against the frame. Therefore, precisely at the point of maximum range of the front wheel retention cable, 4 tons of lateral load are applied towards the inside of the passenger compartment. The test is considered passed if there are no breaks and if the maximum deformation is 15 mm. There are then two tests to verify the resistance of the floor of the safety cell. In one case, 3 tons of load are applied from bottom to top, on the bottom of the frame and at the tank, while another test involves a force of 2.5 tons applied in a slightly more forward position.
A decidedly interesting test is the one it simulates the detachment of the engine from the frame in case of accident. Through the three attachment points of the power unit, the safety cell is anchored to an immobile structure. A torque about the vertical axis is then applied to the frame, along with a force with one horizontal component and another upwards. Both torque and force increase progressively until one of the three mounting points fails, when the procedure is repeated until the other fixings fail. The aim is to verify that the engine supports fail during an accident, without causing damage to the safety cell.
In yet another test, a fake front impact structure (the nose) is mounted on the chassis, which in the 250 mm closest to the body must be the same in specifications and construction as the real one. Simulating an accident that could tear the nose off the safety cell, a transverse load of over 6 and a half tons is applied to the side of the impact structure, without any failure in the body or in the attachment points for 30 seconds. However, the tests for the safety cell do not end here. For example, you press against the walls of the body with a force of up to 30 tons, which the chassis must resist without giving way for at least 5 seconds. In another test, however, 5 tons of lateral load are applied at the height of the upper contour of the passenger compartment, with a maximum allowed deformation of 1 mm after 1 minute.
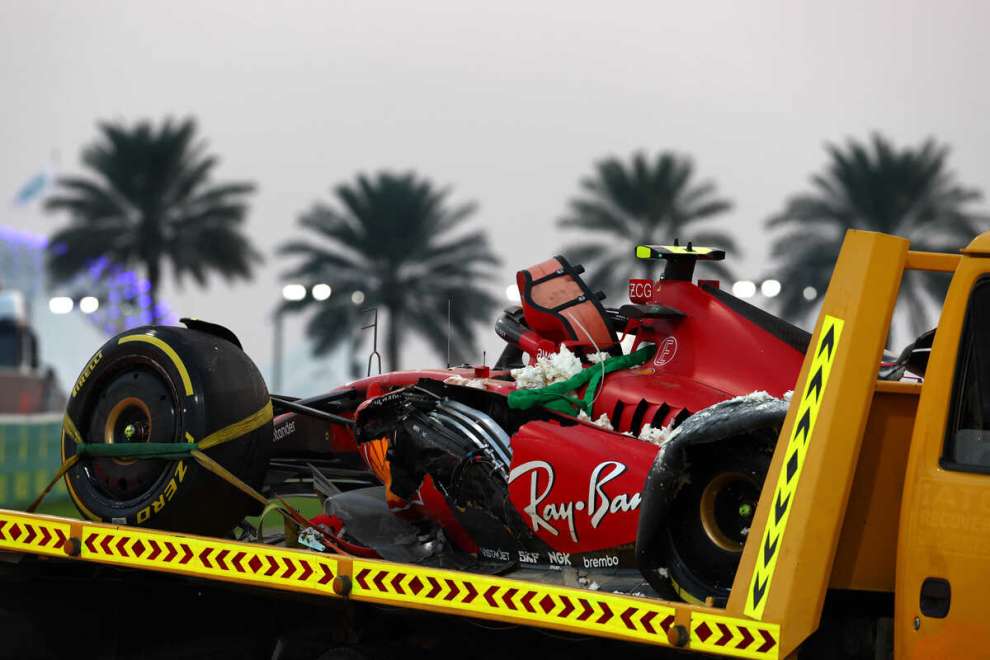
Front impact structure
Another class of checks concerns the front impact structure, a technical term which identifies the nose mounted in front of the safety cell. Also in this case a real crash test is planned, with an impact between a trolley and a wall at a speed of no less than 61 km/h. The nose can be fixed to the wall or to the trolley, for a total mass of the parts in play of 900 kg. The maximum peak deceleration is 40 g, but no more than 20 g prolonged for more than 15 milliseconds are permitted. Furthermore, to pass the test, there must be no damage to the fixing points with the safety cell.
As regards the static tests, a test similar to that already carried out for the safety cell is repeated, simulating a tearing force of the impact structure from the frame. For 30 seconds a lateral force of over 6 and a half tons is applied to the nose, during which there must be no damage to either the structure itself or the attachment points. The final test simulates a load applied to the front wing, with two 400 kg forces, with both vertical and longitudinal components, applied at the height of the aileron. Once again, there must be no failure in the impact structure during the 30 second test.
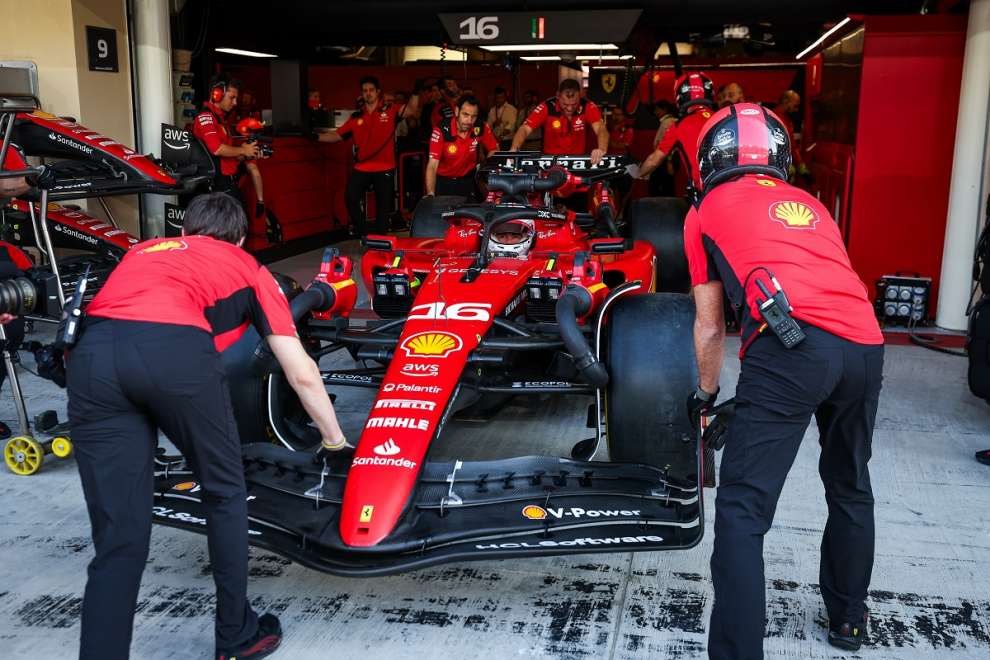
Side impact structures
On both sides of the safety cell there are two impact structures to protect against lateral impacts, also known as anti-intrusion cones due to their oblong shape, vaguely similar to a tube. In this case, the tests are purely static. On the upper structure, for example, an equivalent force of 4 tons is applied horizontally and directed towards the rear. On the lower cone, however, the load reaches 6 tons, to which is added another of 3 and a half tons directed upwards. There are also plans “crushing” tests of the safety cell, applying inward lateral forces of 10 and 15 tons on the two cones. All the tests described last 5 seconds, during which no damage should be reported.

Rear impact structure
Another safety element in a Formula 1 car is the rear impact structure, mounted behind the gearbox. This element is also provided for the classic crash test, where the rear structure is coupled to the transmission, the engine and everything that can influence its resistance. The impact structure is rigidly anchored to the ground, against which a trolley with a mass of 900 kg crashes at a speed of at least 40 km/h, for a maximum permitted deceleration of 25 g.
There are three static tests, applying an equivalent load of 4 tons to the impact structure from bottom to top, then the opposite, and finally in a lateral direction. During the test, the gearbox is anchored to a fixed structure via the coupling elements with the engine. The tests are passed if after 30 seconds there is no failure either in the impact structure or in the gearbox or in the connecting elements between the two.

Roll bar
The last group of tests concerns the roll bar, the element that protects the driver in the event of a rollover. This is not to be confused with the halo, but is the vaguely triangular structure corresponding to the engine air intake, at the highest point of the car. The tests are all of a static nature, with forces of up to 14 tons applied at various points and with different inclinations. The tests regarding the roll bar have become more severe with the latest regulations, in reaction to the incident that happened in Zhou at Silverstone in 2022. The regulation then provides for further safety checks on other components, such as the steering column and the headrest, whose stability must be verified. Overall, chassis homologation is a long, complex and expensive procedure, which attests to how much attention to safety has grown in Formula 1 over the last thirty years.
#Formula #crash #tests #carried